Andy Roy of Fiddleback Forge joins us for episode #52 of The Knife Junkie Podcast.
Andy and Bob “The Knife Junkie” DeMarco talk about Andy’s start as a hobbyist to full-time knife maker. To date, he’s made over 25,000 knives — and he has personally touched every single one of them!
Andy also talks about the business of knife making and his recent purchase — along with three others of Pop’s Knife Supply — as well as what’s in the future for Fiddleback Forge.
It’s a great interview … one you don’t want to miss. And be sure to check out the gorgeous knives on the Fiddleback Forge Instagram page.
Even though he's made over 25,000 knives, Andy Roy of Fiddleback Forge still touches every knife they make to ensure it lives up to the Fiddleback name. Listen in to my conversation with him on episode 52 of The Knife Junkie Podcast Share on X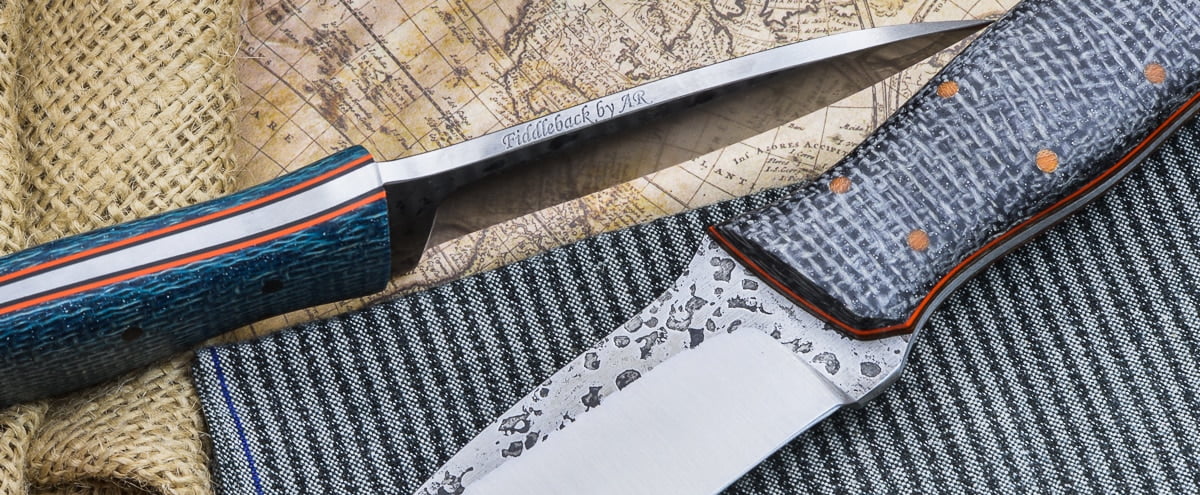
We’d love to get your feedback on today’s show. Please call the listener line at 724-466-4487 or email bob@theknifejunkie.com with any comments, feedback or suggestions, and let us know who you would like to hear interviewed on the next episode.
To listen to past episodes of the podcast, visit theknifejunkie.com/listen.
Subscribe, Download or Leave a Review
Show Notes
Andy Roy 0:00
I like handle work. I do all the handle work we've done over 25,000 knives and I've shaped every handle by hand so I do put a lot of time and passion into the handles the handles they should be comfortable then I should be kind of should be sexy looking knife. Life's too short to carry another knife
Unknown Speaker 0:20
Welcome to the Knife Junkie podcast your weekly dose of knife news and information about knives and knife collecting. Here's your hosts Jim Person and Bob The Knife Junkie DeMarco.
Jim Person 0:33
Hello Knife Junkie and welcome to episode number 52 of the Knife Junkie podcast. I'm Jim Person and I'm Bob The
Bob DeMarco 0:40
Knife Junkie DeMarco, welcome to the podcast.
Jim Person 0:43
Welcome to Episode 52 as we said of the Knife Junkie podcast, it's our weekly interview show a good interview lined up with us today, Bob, Andy Roy, Fiddleback Forge and man I tell you as I was researching and listening to the interview, just amazing everything He's he's involved with not only making the knives but the Georgia knife making guild also a relatively new owner of pops knife supply ... man he's all over the place
Bob DeMarco 1:08
Yeah, well, Andy came on my radar with his fiddle back for mostly on Instagram as a lot of knife makers come onto my radar, but also on YouTube, he produces he and the and the individuals in the shop it's about a five person shop, put out some serious knife I candy. That's what really, that's what really drew me in are these these beautifully refined yet unrefined blades meaning they're beautifully ground but but some of the scale is left on the flats which gives it kind of a rustic look. And then these superb handles. Now I've never held a fiddle backwards knife, but they just look comfortable. They're even comfortable to look at on the eyes. So much attention is spent on the ergonomics and the aesthetics of the handles. Just take Look and you'll see all these beautiful materials, beautiful pin configurations, he goes he goes off the charts with the pins on his knife handles. And that might sound goofy. You know for me to mention as a standout but it is you take a look at his knives and they're striking. Each knife comes through his hands, he grinds each knife and profiles each handle and and he has for each one of the 25,000 I think was the number 25,000 knives come out of his shop. Just Just a few Yeah, just a few you'll you'll hear in the interview but he also is one of these guys the perfect example of preparation meeting opportunity. He had been a hobbyist knife maker and then the opportunity was forced on him to become a full time knife maker and he was ready to go. He had he had a everything he needed for for the start of a shop which obviously built once the company was flourishing. It's it's another one of those American Dream stories, at least from the outside. That is inspiring to me.
Jim Person 2:59
Not only do you have to be ready you have to take this step you have to take the opportunity and man has he ever and his website is gorgeous and as you said the pictures of the knives show the scales if you will or the you know the rustic look and just just beautiful and that's at fullback forge calm you can find all that stuff will have links to Andy's webpage Instagram pumps, knife supply all that kind of good stuff on the show notes which you can find at The Knife junkie.com slash 52 and before we head into that interview with Andy want to remind you that knives 2020 the new 45th edition of the popular knives book is now out over 800 something full color pictures just gorgeous book if you want to find out more you can go to The Knife Junkie. com slash knives 2020 The Knife Junkie comm slash knives to 020 that will tell you that is an affiliate link to Amazon where you can purchase the book in paperback or in Kindle. It's not going to cost you any more. If you use Our link but it does help the Knife Junkie podcast help us keep the lights on here so The Knife Junkie comm slash knives 2020 have a knife you want featured or reviewed, called the Knife Junkie. 24 seven listener line, it's 724-466-4487 and let us know.
Bob DeMarco 4:17
So I'm here speaking with Andy Roy knife maker whose fiddleback forge sets the bar for handmade outdoor and camp knives. And he thank you so much for coming on the podcast. Well, thanks for having me. It's my pleasure. The first thing that really comes to mind when I look at your knives is how they're all the same but different. To me, I went through art school and I was obsessed with drawing portraits and they all looked like me, but a little bit different. Tell me what sets your knives apart from the other outdoor and camp knives.
Andy Roy 4:51
I don't know that. Well, I guess I guess I do have a style that I make knives of my knives. But I don't know that I you know, functionally they're really set apart there, there's some things that I'm passionate about and that I believe, like I can't stand soils so you won't see those on my knives. But, you know I'm an eight inch hunting and fishing knife. Everybody's is pretty good.
Bob DeMarco 5:15
Well, when you look at your knives you really notice the handles, I mean the aesthetics, there's a lot of attention put into the aesthetic. So I have a condor bush Lauren knife and it's a great outdoor knife but there are no embellishments. There is no seemingly no labor or love put into them. You look at your handles, and they are intricate and they look comfortable.
Andy Roy 5:37
I like I like handle work. I do all the handle work. We've done over 25,000 knives and I've shaped every handle by hand. So I do put a lot of time and passion into the handles. When I was a kid I carved walking sticks and so the hand and that was a furniture maker. So the metalwork is what I had to learn. I already knew the woodworking and the adhesives and those things things but the middle work I had to catch up on the handles, they should be comfortable and I should be kind of should be sexy looking nice. Life's too short to carry an opener.
Bob DeMarco 6:09
I couldn't agree more or or an inadequate knife,
Andy Roy 6:13
right? or too few knives. Many knives is better. I mean,
Bob DeMarco 6:17
your knives actually just by definition seem eminently collectible. You might decide that you like a certain pattern for the function and for the way it feels. But you can kind of almost endlessly get in one of those collectors loops and keep getting the same one because the handles are also unique.
Andy Roy 6:37
Well, they are unique. It's funny there there have been some collectors that have collected just one model to the point that just honored to have that happen, but just kind of stand back and it's pretty amazing. You know, we make over 100 models and knives now and
some just lucky that they appeal to some
Bob DeMarco 6:57
Do you discontinue knives or do you have All of those designs kind of active at once
Andy Roy 7:02
I discontinue knives if after a while as I'm making the knife, I don't think it's a very good design. And then recently I discontinued about 30 or 40 models just because of I was just kind of salty, you know, just kind of salted on that model. But some of them are still very good models that I'll go back to someday. But some of them I'm just going to move away from you just kind of got sick of making them. And we've made a lot of them. We've made a lot of them. sound like something fresh.
Bob DeMarco 7:30
You make. You said your hands touch every knife you've shaped every handle, and yet you've made 25,000 knives, how long? You've been around for about 11 years, 10 years, 10 years full time on May 1, that's when I got laid off.
Andy Roy 7:45
So I was 10 years full time and I made nice for a couple of years before.
Bob DeMarco 7:49
What were you doing that you were laid off from?
Andy Roy 7:52
I was an electrical engineer by trade and I was working as a project manager at a company that's on.
Bob DeMarco 7:58
So how how have you managed To make 25,000 knives I know I've seen a number of your fiddle back Friday videos. I know you're not working alone. No,
Andy Roy 8:09
I do the I do the blade grinding and the handle shaping. And so that's the parts that I do and then the you know, so the drilling, the profiling, the sanding, those kind of things are generally done by an employee. At one time we had 11 employees, we were doing 67 nights a week. Well, and now we're doing 20 hours a week and I'm much happier with much fewer employees.
Bob DeMarco 8:32
Yeah, are you feeling the crush? Just keep making knives like I was.
Andy Roy 8:38
I was driven I was driven to just just make more more more. I'm still driven to make my Islam totally addicted to it. I don't think I'll ever stop. Well, you know, as you're my hands are getting old in my eyes are getting old now. I'm 46 OG
it's the starting to hurt a little to midnight. So maybe one day I'll quit. I got to beat buddy. Well, that's alright. Hopefully the podcast doesn't give you arthritis. Yeah, right. Exactly.
Bob DeMarco 9:05
Exactly too much typing, I noticed that you have a number of people in your shop, you seem to cultivate new talent. What's your philosophy on that? It seems,
Andy Roy 9:15
you know, it was weird. I had just gone full time. And Dylan Fletcher showed up and wanted to be an apprentice. And I felt like, dude, you're practicing under a guy that's just learning this this crap. But it worked out and he learned to make knives very fast. And I saw that and I really enjoyed teaching it. So eventually, I just, you know, kept offering that situation and you know, for the business, if I suck somebody into my business as an employee, and they're learning to profile knives and drill knives, the same handles, it's hard to hold somebody in that job. But if at the same time you made him an apprentice, you can keep them in that job a little longer. And it's just really worked out there's I'm kind of impressed when I look back at the different makers that have been through my shop and and through my This program, it's humbling.
Bob DeMarco 10:02
It's like you, you're not just giving them a job. You're giving them hope at the end of it that they can, right? I mean, it's self actualize.
Andy Roy 10:10
How, how else do you break into being an artist and you need to do it all on your own or you are for me, you can come and learn, I'll teach you the whole business, I'll help you. If you lead with your logo, help you get your website set up. I help you tell you when your knives are sellable, and what the market will bear on them. No, that's huge for a craftsman. Just that part, deciding what to sell a nice was a huge thing to be able to come and ask and to know. So yeah,
Bob DeMarco 10:39
pricing of a product. You don't want it too low. Right wanted to high, right? You know, you don't want to prohibitive but, you know, at the same time you're making a luxury item, if you don't mind my saying, like you said you could you could buy a knife at the fraction of the cost and it will do the same job but it won't. It won't have the same soul and it won't mean the same thing to you. Right? And the work you do with it won't mean the same.
Andy Roy 11:02
Most of my knives are carbon steel for that same reason so that there's a mark on their tarnished they those are memories on the steel solo the knife
Bob DeMarco 11:11
so even when you were doing something else before you had this awesome job as it seems from the outside anyway making knives and and and having a successful knife company you were still well hobbyist or were you a hobbyist.
Andy Roy 11:26
I was I did I did knives as a hobby for two and a half years was I was you know in my garage with a forge I built out of kitty litter and a big water trough and I heard one time before that I did furniture and humid doors. I made those I could finish a knife quicker. So I liked that hobby because I could come home for the weekend and get four hours time away from the family and finish a knife and that's you know those are the knives will make the four albums for our that's what I teach my guys we're making a four hour knife you can't do it by yourself and for hours, then you're going beyond what I'm trying to teach you
Bob DeMarco 12:02
soup to nuts even with the even with the gorgeous handle. Oh, yeah. Wow. Well, I can see how that that could be enticing, especially if you Have you always been knife oriented or you hunt Huntsman or
Andy Roy 12:15
by hunt, I shoot my granddaddy collected knives and you know, he was always, you know, catalogs and we would look at the catalogs together and circle one
Bob DeMarco 12:25
could have one on this page which Yeah,
Andy Roy 12:27
yeah, that's Yeah, we did a lot of that. And, you know, the ag rafal catalog. Oh, yeah. You know, we flipped through that all the time. So, and then, you know, I was in it. So that was a nice thing to be able to show him. Oh, yeah.
Bob DeMarco 12:39
Man. It's amazing how many grandfathers are culprits not cold. Or the inspiration of the knife hobby or the knife life?
Andy Roy 12:49
Or I would imagine not just knives I mean that my grandfather taught me lots of cool stuff. I'm sure everybody's the mind was in the fishing and outdoors. But I'm sure that my other granddaddy was In the pool and he was a pool shark and a hot man i mean you know he taught me a little bit of that you got
Bob DeMarco 13:09
you got both angles you got the the slick urban and the cool outdoorsman
Andy Roy 13:15
right nice and then none of mine were into cars I'm sure there's tons of guys whose granddaddy taught them all about cars
Bob DeMarco 13:21
well i think that generation You and I are similar age and so our grandfathers are probably similar age minor passed away but they were children of the depression you know and and and so self reliance was big and I think that's part of what always kind of drew me to knives was this concept of the man walking around with a belt knife you know capable of doing whatever he'll fighting right or or like starting a campfire right. So all of your stuff is is really outdoors he is that who you find your your biggest clients are people who are out there on campsites.
Andy Roy 13:57
Yeah, yeah, pick up my knives or Woods Bowman, nice weather. The most part I do make some some weaponize and some evil looking eyes defense a town the needle the femtocell, the Bourbon Street Skinner. I mean, you're not you don't skin deer on bourbon. But I think for the most part, they're they're sort of outdoor canonize, which is what I love to do with my knives When I was a boy just bumming around the woods with my K bar.
Bob DeMarco 14:21
They really seem to be appreciated. In other words, you're using that knife to skin an animal. You're also going to appreciate the experience of hosting it and using it.
Andy Roy 14:34
I think that's the point I'm making them comfortable and beautiful so that you're you know, sometimes you just take a break from the work and look at the knife and smile.
Bob DeMarco 14:41
Yeah. So you some crazy my card is I've noticed my card is just about my favorite handle material. I love it mine too. I've been replacing a lot of my pocket knife skills with my card if I can find them.
Andy Roy 14:54
It's indestructible. You know, and it's I find it to be lovely. I've I've always like to mix it in even you know even when the weather would handle it. If the pollsters are McCart I love that. Just like that. I love the McCarter pins, although a lot of that is about making the knife easier to make. But I love those McCarter pans I think they look great.
Bob DeMarco 15:13
Yeah, you made the oddly placed but there are many pins on your knives. Did it on pins all over them. I love the way that look. I had I
Andy Roy 15:24
had a guy when I was first making knives told me that you get stupid with the pins doesn't look professional. And I just went crazy. And I put pins everywhere on the knife after that. Yeah, I fight those kinds of restrictions. Well, yeah,
Bob DeMarco 15:37
that's absurd.
Andy Roy 15:38
But a lot of that was just about making the knife easier to make the McCarter pins they never sand proud of the handle material. You never you never feel that bump and they never burn you know the handle material. You know the Bernie ones especially like maple and Osage, you know, put a metal pin in there UE overheated or God God forbid a copper pan and then You overheated and it makes a little black halo around the pen and McCarter pens never do that. So a lot of that was just to make them life easier to make
Bob DeMarco 16:09
interesting. It ends up being kind of a signature look for you. It kind of worked out that was kind of goofy. Wait so so when you overheat a pin, say and it's in a Bernal would like you mentioned Osage for instance, does that also weaken the integrity of the glue holding it in the box? I
Andy Roy 16:29
would imagine it affects the glue. Yes, I would imagine it does. The glue is not meant to get that hot. Their specs on glue bottles, you know, they work from this range to this range and then they break down. So I would have imagined so
Bob DeMarco 16:41
So how long did it take you? So you just kind of just started making knives you you were in the garage for two years as a hobbyist and then you got laid off and you said this is my this is my chance. And you started what was your learning curve like when were you producing knives that were worthy of the fiddle back name or your name?
Andy Roy 17:04
Well, I had been making and selling knives under the fiddle bag name for a couple of years as a hobbyist. I had a full shop, everything was up. Okay, the website was there. For the forum pages were there, the Instagram was there. So I just got laid off and my wife has the better job. She's got the best career so we weren't going to move for my career. And I called her and I said, Look, I got laid off and I'm going to be a full time knife maker. And she didn't have a lot of supportive things to say about that plan. But over time, she's become more supportive. Well, yeah, and she didn't say get out. So
Bob DeMarco 17:41
I'm sure that does happen.
Unknown Speaker 17:43
Many knife makers let me say
Bob DeMarco 17:45
you're going to do what?
Unknown Speaker 17:46
Yeah.
Bob DeMarco 17:48
So this learning curve with with materials and forming your your, your overall look, was that kind of locked in once you started? I mean, obviously it was preparation Meeting opportunity and you were ready to go. But once everything was on the line, how did that change your life making?
Andy Roy 18:07
I don't know, I just think I got a lot more practice right away. You know, I went from making 10 or 12 knives a month to 10 or 12 knives a week. And also pretty quickly, I figured out that, you know, those nights at 10 or 12 nights a month, I had all this demand or I thought I had all this demand. And then I went full time and I just quadrupled that amount of knives. And my demand wasn't what I thought it was when I made the supplies four times as much so there was a lot of just scrapping this. We're going to sell this week, we're going to make a pretty I'm going to make them better, you know, how can I make them more consistent and faster. That's how the spotted steel came about that pattern is on the flats of my knives. That again is about making a knife easier to make if you texture the flats of the knives, it's way easier to finish the flats of the knives you only have to finish the high spots. So that once again was about making it more efficient to make the knives Doing all you know all of it myself.
Bob DeMarco 19:02
So forge is in your name. How does how does that play out?
Andy Roy 19:06
It was an internet handle that I had when I started making knives and I was I was for denies at that time I might have forged, you know, 10 knives in my whole career. And then I figured out Well, it's a lot more efficient to do these bar stock. Okay.
Look, I know exactly what that steel is.
Bob DeMarco 19:26
Right? That makes it makes sense for for your kind of output. So now 11 years into the game, you're you're you're humming along is is how it looks from the outside anyway. And it seems like you have a really good thing going you have a tight crew. You have this Friday night fiddle back release video, which is really cool. I want to talk about that. But I'm going to tell you what my pics are from the last one. I like the word hug, which I know is a big one. Yeah, the car one and then the needle and the Gun Stock
Andy Roy 20:00
Those those are all new designs. You know, since I got salty on those old ones, I threw me out I drew 30 new knives. And those are all the picture brand new designs.
Bob DeMarco 20:12
So so you're not a custom knife maker, you are a maker of handmade knives. And and you have a very interesting way of selling I think the throwback
Andy Roy 20:21
Friday I just thought of I thought of the marketplace sort of is that you needed to feed it regularly, like a pad or something. And the fiddle back Friday, we just kind of stumbled into that. I think I think actually the guys on the forum voted to have the sale on Friday. And then the name popped out. I don't think I made up the name, I think it was some guy on the forum made up the name. And we've just kind of run with that. It's really neat because there's not a lot of jobs where you work all week. And then at the end of the week, you get to see the exact results both both you know physically and economically of your work. And generally people are giving you you know, comments and criticisms mostly compliments, you know, a lot, not a lot of people that hey, you did so good this week, things are beautiful. So it's, that's one really rewarding part of what I got set up.
Bob DeMarco 21:10
Yeah, that's true. Actually, most jobs, you don't see either what you're doing or producing, or what the effect is. And most of the time, you don't see both of those things. And that can be you know, demoralizing, but having a direct relationship with materials and then the goods that you're churning out, right. And the community around it, too. I mean, I've been doing it 12 years, these guys, you know, customers, they traveled down here for blade show, and we do a bunch of events down here. They travel down for tons and tons of events. And
Andy Roy 21:43
so there's a community around it. It's it's really humbling and amazing.
Bob DeMarco 21:49
So how have you seen the knife community react to you over the years as you've as you came in and made a name
Andy Roy 21:57
kind of crazy. The knife community is The most open our arms community of people that's just been accepting from the start. gone nuts. Even when I came in, you know, when I came in and I'm making full time, I think my knives looks terrible and 2009 when I went full time, but they were settling and you know, I was in the Georgia knife makers Guild, and those guys never wants acted like they were irritated or busy or any of that they just welcomed me with open arms and I learned I've learned a ton being involved with the Georgia mapmakers Good
Bob DeMarco 22:32
to have you mentored with anyone that you're mentoring other young young talent, or new talent, I should say, I don't know how young they are all over the spectrum. So are you being do you do you have certain people you look to for mentorship?
Andy Roy 22:45
Oh, yeah. Tom crime was Dan Koster. And Scott Guzman, were these are guys that took my questions again and again and again. And then you get into the Georgia guild and you're looking at car wreck Steiner, john short, Scott Davison Dennis Bradley these guys just have taken questions again and again and influenced and helped me watch me not take their advice and still put up with me. You can't be involved in this community you know, and now I'm in the you know, the the knife makers guild as well and voting member in that organization. You're surrounded by Todd bag and you know, all those great makers from Texas. So amazing community to be a part of,
Bob DeMarco 23:28
what are your feelings on the Chinese market? The high end manufacturers? I know a lot of makers and designers go to them for OEM work to produce more affordable versions of their knives but at a high level. What do you think of that new force in the market over the last five or six years?
Andy Roy 23:52
I just you know, if you can, if you can bring a product to market that you can sell, got nothing, no problem with you. I'm not having that done with my nice but if somebody made an offer and the thing worked out I don't know that I wouldn't. Like I said a business is hard when I businesses a hard business. And if you bring a product to market, you're out there in the ZS, talk about selling it and you can culture, enthused enthusiasm and a group of people then more power to you.
Bob DeMarco 24:19
Yeah, I got no problem with that. You have a mid tech line. What is that?
Andy Roy 24:24
It is it was the idea was to try and make a line of knives that I didn't have to put in any of the physical work on I could do sort of an intellectual property line and knives and my crew that I already had there and trained up could actually manufacture that line a nice, it didn't really work out. I think there's a lot of good knives there and everything but never was super profitable. So I've tried a couple of things like that medtech where most of the stuff was done on machines and then I did coming played works USA where it was all handmade, but it was my designs and they were making a In the shop, but really the federal back knives are what sells and yeah, so the just as what it is,
Bob DeMarco 25:07
well those medtech knives are actually good looking and man they're
Andy Roy 25:10
always knives they are
Bob DeMarco 25:12
especially the the smaller the two machetes, man that is beautiful.
Andy Roy 25:16
Now we still do them, we still need a machete significantly. I think the machetes are just too good not to do.
Bob DeMarco 25:22
I think it's a really interesting idea that that you were doing a mid tech within your own shop. I mean, that's, that deserves a different kind of name because I always think of the term medtech as everything out sourced and then coming to your location and you like putting it together and and fine tuning it but in but you're doing the whole thing. It's just not your hands. It's right, our assistance hands and
Andy Roy 25:46
so we tried it one way then we tried another way. Neither of them worked. I'm going to keep trying. No they say they say successful people just keep trying till they succeed. So you know,
Bob DeMarco 25:55
yeah, he's roll with the punches. Good idea. Good looking knives. Really cool. idea of how to produce it. It just wasn't that that time at that point.
Andy Roy 26:05
Yeah. And never can tell. There's so many good knives out there right now that it's a it's a tough business knives are challenging.
Bob DeMarco 26:13
So, uh, do you keras anybody else's knives?
Andy Roy 26:15
I got a vast collection of knives. The one I'm carrying right now is by Russell Reese one of my apprentices. You gave it to me the other day and I've been carrying cutting boxes at pops. So yeah, I carry
Bob DeMarco 26:28
other guys knives all the time. You were influenced by someone and now I can't remember his name but but you were showing off the handle and how it's got a it's got a little swale in the back. So it makes like the perfect little three to four handed grip. I think you've picked up one of his knives at blade show or something like that as car wrecks, diners nice, Carl Rick Steiner. Oh, the car one right and CR one right. Okay.
Andy Roy 26:55
Yeah, I am loving that. You've been doing something Interesting things with handles lately, like with the gun stock with the CR one. And then there was another one that was even smaller. It was almost the size of the runtime I believe with. There's another new one out that's called the snow veil. And that was that was influenced by Bill snow, another Georgia filmmaker, and he's been making that knife for 50 years. So it looks like it would be the funkiest thing and the most uncomfortable uncomfortable thing in your hand. But really, it's just it's on your hand like an oval and it's amazing little hand I showed it to a guy at the show. We were at this weekend with pops night supply, and the guy looked down at it and he goes, I've been wanting to see this in person and he holds it. Okay. Wow. So I find it challenging to take the ugliest shake and see if I can make it go. I've drawn a couple in this recent batch that are just ugly and dumb. There's one that looks like a shark eating a little minnow or something. But it comes out so I'm only going to make four or five of them but it comes out so comfortable in my hand and the point is in just the right spot, so I kind of want to Kind of like the goofy thing
Bob DeMarco 28:02
well actually that I was gonna say that handle intuitively looks comfortable to me like it looks like like that little hump towards the back would would nestled nicely between my I know you talk about putting the finger right on top of it but my my hands It looks like it might fit and you know with the pinky on the outside giving it a little bit of control and closure it just looks like a comfortable handle. Always try
Andy Roy 28:26
and make it where then the handle you can hold the handle more than one way and there's a lot of different ways you hold a knife you know you got the steak and just liver thing although yes crafters talk about I can't ever find a
Bob DeMarco 28:40
reverse chess pull. Yeah. So you have this Barracuda that also has an interesting handle. Almost looks like a fish tail. Yeah, that's it right there now, but it also I mean, to me there has to be some utility in that and it looks like the it looks like it's it's built for a whole bunch of different handholds.
Andy Roy 29:00
It is it's a very, it's a wide open handle. I learned from the guys on my forum that you can have a five inch handle, but you've only got three and a half usable inches because there's so many, you know, back since outside the shape of the handle. But this is a wide open handle. So it's a full five inch handle and it's wide open. So if your hands are even wider than that, and believe it or not, I get guys with massive hands have had to design some goofy looking knives to go with these massive hand. But this one's wide open. So you know, never closes off your fingers can fall off the end without it being uncomfortable, you know if they're eight inches wide.
Bob DeMarco 29:37
So what is your what's your overall design philosophy? How do you how do you approach knowing that you need to work on another model? How do you approach what that model is for and what it looks like?
Andy Roy 29:51
I'll generally pick a function and a size factor. And then I'll design I always start with the spine of the knife and I'll draw something And then I'll based on around and I'll do six or so on a page. And then once I get something that I kind of like I always redraw it on a separate page and try to get three or four more models out of it at different sizes. So it'll go all the way down to the right size, and then all the way up to the Duke size. And out of that, you'll get some that really work and some that really don't want to try to reshape the spine and start over.
Bob DeMarco 30:27
So with your motive releasing knives, or selling them, is that a direct? Do you get direct feedback? In other words, I'll make a small batch of this new knife and and see if it works in the hands of the people who use them. Do you do you operate like that?
Andy Roy 30:44
Oh, yeah, I mean, I watch that forum a lot. You know, they those guys are smart. They really have stuck their enthusiasm. It's it's the enthusiasm that just amazes me and like that usable handling concept. I didn't learn that from a knife maker. I learned that on the forum them they had sketches Here's the handle men and then here's the usable handling. They were wrong, you know, so you gotta you gotta look at the feedback knife makers get a lot of
Bob DeMarco 31:12
I wonder if wrench makers get as much feedback or clamp.
Andy Roy 31:18
I can make a sexy Grinch.
Bob DeMarco 31:21
That's the whole thing like it's that you know knives have sort of intangible appeal. Wood that goes beyond a tool and it goes beyond weapon. By the way I like that you dabble in in weaponry because I love weaponry.
Andy Roy 31:37
Very dabbling very dead. I like the stupid stupidest weapon. I like cavalry sabers.
I mean, the French and English cavalry savers like those big the kinda used to Waterloo with the big Yeah, saber with a fat huh the British 1796 is what I really want to be able to make Okay, it's so challenging. It's ridiculous the blade is so we'll see. I made I made my first sword and broke the tip off before I got the handle on it
Bob DeMarco 32:11
when you made your first sword so do you make swords any certain regular I was
Andy Roy 32:15
working on it we recently me and three partners bought pops knife supply so it kind of cut into my dabbling in the swords. But at the time I was trying to put a saber together and I ground it out and fit the basket handle to it and carve the grip and send it out and got it he treated and got it back and broke the tip off.
Right in front of everybody in the shop
Bob DeMarco 32:39
that must have been before we get I want to hear about pops knife supply, but before we do, I just want to follow up on the needle. Tell me about the needle.
Andy Roy 32:51
Sometimes you just draw a knife and then you try to try to make it super super. I like to do this. I like to try to make it ridiculously skinny and then What if the needle came from that Gun Stock? And the back of it as you look still has that guns curve just like that little curve on the back and said, Well, let me just put that back there and take everything out of the width of the knife and make it absolutely as point.
And that's where that came from.
Bob DeMarco 33:16
That little swale in the back of the handle that you like, actually seems like it would aid in thrusting, like, like it would Nestle into the root of your poem here.
Andy Roy 33:25
It might that was one of my ideas or you know, maybe it maybe it would I mean, it is so sharp at the tip. It's ridiculous I get them I lay them in these trays, and then I'll turn around and use my finger and it'll lift one out of the tree to pick it up some operation Well, this thing was already sharp and it went directly through my fingernail. I mean, I've done a lot of nice and it just suck through my fingernail like it wasn't.
Bob DeMarco 33:50
Does that thing have a cutting edge? Oh, yeah.
Andy Roy 33:53
Okay, what's the point of making a night? Yes,
Bob DeMarco 33:55
exactly. What well the point it does look like an assassin stiletto from like,
Andy Roy 34:00
Oh, it has a cutting edge.
Bob DeMarco 34:02
So pops knife supply you you casually drop that you just bought that. What is that?
Andy Roy 34:07
Oh well pops nice supplies been in business for 40 years James parks pop and started almost 40 years ago and he just wanted to retire and he was right around the corner from us. So me and I got some partners together we bought it. Throw it in the shop.
Bob DeMarco 34:21
So is it you sell supplies to knife makers, or is it just a knife shop?
Andy Roy 34:26
know it's just it's supplies? The knife makers,
Bob DeMarco 34:28
right? I'm sure all the knife makers are cringing right now. I'm sure it's it's something everybody knows about. So sorry.
Andy Roy 34:34
Sorry. Sorry. It's been a lot of fun.
Bob DeMarco 34:38
It's busy. Busy. Oh, man. Well, that's good news. And it seems like the knife world is burgeoning. I think AutoCAD is a great What do you want to call it leveler of playing field? I feel like people who who've never lifted a hammer or I guess that's a symbolic camera is someone who's never approached a grinder can if they can use AutoCAD can have a knife made and I think that's pretty, pretty amazing.
Andy Roy 35:08
Yeah, me too. I guess it's definitely a
I call it a renaissance of craftsmanship. I think we're having not just knives but we're definitely I mean, the knife steals that we have now. They're amazing. You know the handle shapes the variety, the hundreds of hundreds and hundreds of makers blade show it's so crowded and I don't know if anybody there's a knife fire anymore. They're all knife makers. So there's a renaissance of craftsmanship going on. I think it's a I think it's because our wives work. I don't think I actually think most of the renaissance of craftsmanship is because the guys were able to do this stuff in their garage because their wife works and they get the insurance for me that was what it was. And I got all the knife makers I know have wives that can get insurance for the DI in a bad way.
Bob DeMarco 36:00
Yeah, yeah, I know exactly what you're talking about. Myself and most of my friends are all in that similar boat. Yeah. Interesting. That's the first time I've heard that because I, I've talked a lot with a lot of different people about how the knife world has expanded, just under my, this is gonna sound corny, but under my watch, that means for as long as I've been paying attention to it on YouTube, I've always been a knife collector since I was little, but I guess my first nothing fancy video in 2008. And it's exploded since then
Andy Roy 36:36
praising when I got into it, you had, you know, three or four choices to get a grinder? You know, you got a Bader or there was three or four choices squeal and square wheel and now you could research grinders and have a spreadsheet of 100 different choices and that's not all of them.
Bob DeMarco 36:53
So where do you think it's all going? Do you think? Do you think it becomes a crowded field as a crowded field when mounted on much it is a crowded field as a completely fixed blade maker. Yeah. How do you see that market different from the folding market?
Andy Roy 37:09
Well, I think the folder market there's a, there's more lucrative style buyers. If you know what I mean, you know, there's people spending more money on just people spend my money on there's a lot of variety in the two to $5,000 folder market. And really, I mean that you narrow down a lot in fixed blades when you get that high up. There are fixed blades that expensive but there's not, but it is it's crowded out here right now. I think the TV show has a big, big effect on
Bob DeMarco 37:39
Yeah, forged and fire. I think also that folding knives are people consider them eminently more variable. And I guess maybe they are in terms of legality and stuff. But this is not a an attitude I espouse but if you're a knife enthusiast and you're not getting in trouble with the law all the time, sometimes times you might want to carry a fixed blade or, you know, I myself do. And it's not necessarily legal Unless Unless I'm wearing it out. And I don't I'm not comfortable with that. So I don't do it that often.
Andy Roy 38:12
Right. And what state are you in? I'm in Virginia,
Bob DeMarco 38:15
okay. Which oddly enough has some pretty old school knife laws old school meeting, like I would think an old school state like Virginia wouldn't have many restrictions, but we do and they're ridiculous. We got to get Doug Ritter on Yeah, I've had him on the show a couple of times. And and he he came on, right after our ridiculous governor decided not to sign switch bills into legality switch blades into legality. Yeah, he had just gone through that blackface thing and was all embarrassed so didn't want to raise any hackles with a with a switchblade legislation. Yeah, he's an amazing guy. I'm glad
Andy Roy 38:52
he's he got so much done here in Georgia. I think the law is kind of silly. You're allowed to carry a knife with up to a 12 inch blade. without a permit
which is ridiculous. Okay. carries. Yeah, exactly. Why didn't they allow me my cavalry saber?
Bob DeMarco 39:12
Right? I mean, presumably you get a permit for everything over 12 inches right I mean, you know Yeah,
Andy Roy 39:17
yeah, I could get a permit carry my cavalry say yeah,
Bob DeMarco 39:20
it should be covered under your CCW. Yeah. Well so where do you see fiddle back forward headed in the future?
Andy Roy 39:27
I just think I'm going to design more knives I'm going to keep teaching knife making I love to teach it that's it. I'm just gonna keep making knives. I love it. I love making I love designing them. I love taking it from design to a product. So I just figure I'm just going to keep on truckin.
Bob DeMarco 39:45
Do you have a favorite of your own model
Andy Roy 39:47
right now I love that new Shogun and the fillet knife I've never done a fillet knife before that fillet knife I've got right now that handle is so good. I love that knife. It's going to be I've really enjoyed it. So we're going to release the first couple this Week, but those two new models the Shogun and the fillet knife I figured the handles are as good as any I've ever done.
Bob DeMarco 40:07
So with the with the fillet knife was learning to grind something that thin and flexible. Was that already in your wheelhouse? Or was that a learning curve to get there?
Andy Roy 40:16
It's funny. I've learned from Joey very really my one of my newest apprentices and he's in the shop and he just kitchen eyes and he's just unbelievably good at it. And you know, kitchen knives are the hardest fixed blade knife to make the the high grind on very hard stainless on the very hard steals very, very thin edges. These things make the knife complicated to make. So he's very good at I'm just been watching them and I'm thinking
Bob DeMarco 40:44
I could do that. So no doubt, no doubt you could and you put a beautiful handle on it. The handle scope
Andy Roy 40:51
that I can do.
Bob DeMarco 40:53
So where do where do people find your knives? Where can they see them? Where can they buy them?
Unknown Speaker 40:57
Well we use a whole lot of dealers. They're all on the fiddleback forge website you can get them from our website. There's user markets at Facebook but you know Old Town cutlery DLT knife ship free, the knife connection, these cutlery. These are all there they're all those dealers have my knives and more and they're all listed on this fiddleback forge website.
Bob DeMarco 41:17
And you can also go right to your website. Yes by and and it is
Andy Roy 41:22
a purchase from a dealer is a purchase from the knife maker. So support the dealers to absolutely.
Bob DeMarco 41:29
So let me just ask you before I let you go, Okay, do you have a knife story? You could regale us with something funny? something scary. Something anything?
Andy Roy 41:41
I have a lot of broken knives.
I tend to break a lot.
But you know No, I don't know. I spent my whole childhood bumming around with the K bar night but every time I think I got in trouble that wasn't what that wasn't the cause of the trouble.
Bob DeMarco 41:59
Like it bump Going around childhood with a K bar now Spoken like a true nice guy. Yeah. Well Andy Roy of Fiddleback forge it's been a pleasure speaking with you thank you so much for coming on the Knife Junkie podcast right thank you. It's been my pleasure and now having spoken with you, I'm going to feel an imperative pull to buy a needle or a car one or something but probably the needle that like kind of my style
Andy Roy 42:26
Cool. Cool. Show me pictures when you get it. I will indeed
Bob DeMarco 42:30
I'm going to get it with that Maroon handle that you showed off last week that was bad awesome bad very good of course.
Already sir. It's been a pleasure thank you very much.
Announcer 42:39
Subscribe to the Knife Junkie his YouTube channel at The Knife Junkie. com slash YouTube
Jim Person 42:47
Back on The Knife Junkie Podcast, Jim Person along with Bob The Knife Junkie DeMarco and interview there with Andy Roy from fiddleback forge Bob, what what were your thoughts key takeaways?
Bob DeMarco 42:56
Well, knife making proves to be quite a solitary activity. From a lot of the people we talked to, it's a lot of hours hold up alone in your shop, toiling in obscurity until you burst onto the scene. And, and the story is a little bit different because he has like a couple of other people we've spoken to recently. He has a small shop, and he everything that goes out of his shop touches his hands, you know, he has a major role in forming each night. yet he's surrounded by three or four or five workers and apprentices and other nice people who are helping him in his venture. And he in turn is helping them in theirs, you know, with with his apprentice program and with encouraging the encouraging the knife makers that work with him to pursue their own careers like the gentleman he mentioned with the who makes the kitchen knives, which is an incredibly difficult pursuit. To me. That's the old school and proper way of going about business. Not that there aren't other proper ways, but that whole idea of bringing in newer generations new We're talent and cultivating it and encouraging it while you're getting labor on your own project. So everyone kind of wins here. You're lifting up the next generation, if you will. But you're also being lifted by that generation as you try and output the production you're looking to output. Right? win win for everybody. Yeah, just seemed like a cool guy seems like a great place to work and you were mentioning OFF AIR Jim about how he had a recent gathering a hammer and I think it his, his shop, his shop looks so cool. One of the things I love to do is look at famous artists studios, and famous knife makers shops, and his shop just looks great. And it just looks like a great environment. So just another person I've spoken with where I'm getting clues on what my future life will be. And future road trips are and future road trips. Indeed, he's, he's down in Georgia, and, and I've never been to Georgia, one of the states hadn't been to so
Jim Person 44:57
really well Blade show is coming up ... road trip?
Alright thanks everybody for listening to Episode 52 of the Knife Junkie podcast for Bob The Knife Junkie DeMarco I'm Jim and I've newbie Person. Want to thank you for joining us and be sure to catch us again mid week for Episode Number 53 of the Knife Junkie podcast.
Announcer 45:16
Thanks for listening to the Knife Junkie podcast. If you enjoyed the show, please rate and review it review the podcast com for show notes for today's episode additional resources and to listen to past episodes visit our website The Knife Junkie. com You can also watch our latest videos on YouTube at The Knife Junkie. com slash YouTube check out some great night photos on the Knife Junkie. com slash Instagram and join our Facebook group but The Knife Junkie com slash Facebook and if you have a question or comment, email them to Bob at The Knife Junkie. com or call our 24 seven listener line it's 724-466-4487 and you may hear your comment or question answered on an upcoming episode of the Knife Junkie podcast
Past Episodes
Catch up on past episodes of The Knife Junkie Podcast.
Subscribe to the podcast in your favorite podcast player or by RSS so you automatically receive each new episode.
Join The Knife Junkie community and we’ll email you when a new episode comes out so you don’t miss anything.
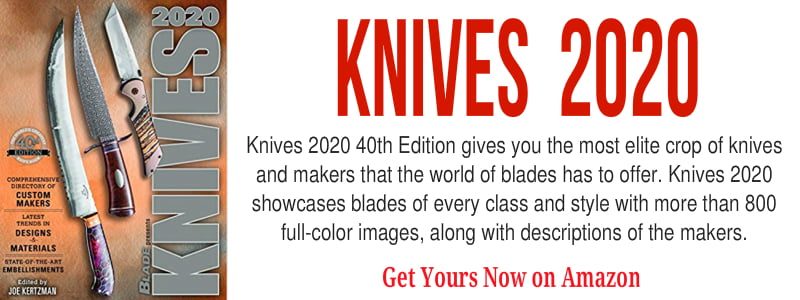
Shopping for a Knife?
Support The Knife Junkie Podcast and YouTube Channel by buying through my affiliate links
Shop on Amazon
Shop on eBay
Shop on Blade HQ
Shop on Field Supply
Shop on Knives Ship Free
Follow The Knife Junkie
Visit The Knife Junkie website
The Knife Junkie Listener Line — 724-466-4467
Email The Knife Junkie
Follow The Knife Junkie on YouTube
Follow The Knife Junkie on Instagram
Follow The Knife Junkie on Twitter
Join The Knife Junkie Facebook Group
Affiliate Disclosure
In the name of full transparency, please be aware that this website contains affiliate links and any purchases made through such links will result in a small commission for me (at no extra cost for you). If you use these links, I might be rewarded credit or a small commission of the sale. If you don’t want to use these links, no problem. But know that I truly do appreciate your support.