New York Knife Maker Nick Chuprin — The Knife Junkie Podcast (Episode 102)
Nick Chuprin, New York knife maker, is the featured guest on episode #102 of The Knife Junkie Podcast. Nick began collecting knives at 13 and started his own knife business at the ripe young age of 17!
He funded his knife shop with the lotto and had to rebuild his initial set-up following Hurricane Sandy. Later he purchased a Haas CNC milling center, after spending about 9 months learning the code and how to program it — and now utilizes modern technologies to create a wider range of products.
He also talked about some of his collaborations as well as his own podcast called “Bladeology,” hosted by Chuprin (The Maker), Jeremiah Burbank (The Dealer) and Elijah Isham (The Designer) — and announced a new partnership called Syndicate Blades.
Find him online at NCC Knives as well as on Instagram.
New York Knife Maker Nick Chuprin, who started collecting knives at 13 and began his own knife business at 17, is featured on this week's The Knife Junkie Podcast (Episode 102) Share on XPlease call the listener line at 724-466-4487 or email bob@theknifejunkie.com with any comments, feedback or suggestions on the show, and let us know who you’d like to hear interviewed on an upcoming edition of The Knife Junkie Podcast.
To listen to past episodes of the podcast, visit theknifejunkie.com/listen.
Subscribe, Download or Leave a Review
Show Notes
* Transcription is generated by artificial intelligence (ai) and is not edited. There may be some errors. Thanks for understanding.
Nick Chuprin 0:00
I was a perfectionist I am a perfectionist. I'm not only perfect types no one does but to the best of my capability if I see a scratch or something that I could fix I have to fix it as the right but there are flaws in the flaws are usually like that's the best of a grinder or it's the best I could finish that or if I know if I work if I work harder at the handset it's just gonna get worse because it's gonna be overworked and things like that. But if I made it to the best of my abilities, that that's what I try to do.
Announcer 0:32
Welcome to the knife junkie podcast your weekly dose of knife news and information about knives and knife collecting. Here's your hosts Jim Person and Bob The Knife Junkie DeMarco
Jim Person 0:46
Hello Knife Junkie and welcome to episode number 102 of The Knife Junkie podcast I'm Jim Person
Bob DeMarco 0:52
and I'm Bob DeMarco. Welcome to the show.
Jim Person 0:54
The Knife Junkie podcast is the place for knife newbies and Knife Junkie is to learn everything About knives and knife collecting and we get to hear from the knife designers, the makers, the manufacturers, the reviewers. Anybody who loves knives Knife Junkie podcast is for you and a great guests that we're going to hear from today, Bob. But first we have a couple of special announcements we talked about last week on our episode number 100. A couple of special things you we're going to be doing a knife giveaway and celebration of that 100th episode.
Bob DeMarco 1:25
That's right. Anyone who has listened to this show or seen any of the videos knows that I'm a huge fan of the cold steel broken skull for its slender long bladed super steely you know, you can have it on you at all times. It's so it's so feather light and thin so I decided what better knife to give away than a broken skull. As you know, I like to carry pink broken skull for cognitive dissonance but in this case, I'm not going to force anyone to carry pink. So I got an od green broken skull and I'm going to add the snaggletooth mF to it and other snaggletooth m f is the aftermarket pocket Deployer from snaggletooth tactical, a great New Jersey company. And this thing allows you to basically wave knives out of your pocket, if you will, a bit like an Ernest Emerson, an Emerson wave knife. So it's a great aftermarket product. It's a great American company, and of course, Cold Steel. You know how I feel about them. So we asked people to email me with Episode 100 or 100th episode in the subject line, and they would immediately be entered into a random drawing. That's right. And so we're going to do that random drawing.
Jim Person 2:37
Oh, wow. Okay, so you actually didn't do the drawing. Okay, I thought you might have had the winner already picked. But
Bob DeMarco 2:42
oh, that's exciting. We're gonna do it right here. Now. I've done this before@random.org true random numbering. Now these people really take randomness seriously, it's kind of a scientific thing for them. So I decided why not, why not put them in. So I have a list of 20 g7 entrance
Jim Person 3:01
so as every email came in, you assigned it a number
Bob DeMarco 3:04
I assigned it, I would shuffle it off to a different folder. And I even checked I checked the YouTube comments too just in case and put them in a list and as they came in, that's a it's a chronological list. And so now I have in the true number generator, I have one through 27 I'm gonna hit generate it's gonna catch a number
Jim Person 3:26
I should have a drumroll sound effect I forgot that. There we go.
Bob DeMarco 3:32
Number 13 and number 13 lucky 13 number 13 is Ben sharer. Oh,
Jim Person 3:39
sharer, congratulations, Ben.
Bob DeMarco 3:41
Oh sir. Ben if you are listening, you won the cold steel broken skull with the snaggletooth mF attachment. I will be sending that out to you post haste. Things are a little slow right now but as they ship they ship pretty quickly so as you know with not too many people sending packages right now so I will get myself into In a situation where I can get to the post office ASAP and get this out to you because you don't want to wait Ben chair so I will also send you an email let you know in my eyes congratulations
Jim Person 4:09
Ben Thanks buddy for for being a listener and on the Knife Junkie podcast and for entering the 100th episode knife giveaway and thanks to everybody else that did enter and sorry you weren't the winner, but you are a winner because you're listening to the podcasts. I tend to agree Jim, a nice second place for you. But hey, if you entered didn't enter we also want to make sure that you join us this coming Saturday. Now this podcast is coming out on Easter Sunday, April the 12th. this coming Saturday, April 18 at noon, The Knife Junkie is going to have a live Saturday knife hangout starting at noon on his YouTube channel and you've already got several big name guests already lined up and you're working on getting more guests. That's right also giving our listeners a chance to join in if they have a way cam they can actually join in the show talk to you talk to the guests show off a knife maybe that they want to sell or whatever. It's just gonna be a fun afternoon and however long it goes, it's however
Bob DeMarco 5:10
long it goes. Well, I just want to tell people this is a great idea that Jim had because we were we were talking about, you know, things we can do instead of, well, knife events that are being canceled left and right. And we thought what a great idea to get some of our friends of the show together, people who come on Thursday night knives and people who we've interviewed here on the show, and just kind of have a knife Hangout, you know, and have it have it last, I don't want to say indefinitely, but you know, we'll go for as long as it goes. I might have lunch here, you know, while we're talking. Who knows? It goes for three hours, and I'm trying to wrangle a very special guest or two. And we'll see if that happens. I don't know. But it would be cool to float someone in that everybody knows you know of and and and what
Jim Person 5:59
Hopefully we can float many people in Yeah, you know, we're really hoping that this can be a like set a chance for a lot of folks in the knife community to come together and just chat you know, maybe have a few interviews as you said during the course of the show get a chance to meet different folks have listeners or viewers come in, show off some of their knives, sell a knife, whatever. So, yeah, I'm looking forward to it.
Bob DeMarco 6:23
Yeah, me too. Everyone has to show up. I'm gonna have everything around me. All of my knives arrayed around me just in case something has to be pulled up
Jim Person 6:31
and a porta potti so you can keep going. Yeah, one promise this won't be 24 hours. Yeah, there will be no bed pants lesser. Alright, so again this Saturday, this coming Saturday, April 18 at noon, that's on the knife junkies YouTube channel that you can find at The Knife Junkie. COMM slash YouTube. If you are not yet subscribed, please go there and subscribe now so you'll get a notification when he goes live on Saturday. But also this Thursday and pretty much every Thursday as The Knife Junkie goes live with Thursday night knives, and that's at 10pm on Thursday, so a couple of chances this week alone to catch you on video as well as the Wednesday audio podcast. So it's Knife Junkie all around this week. Oh, yeah, yeah. Spread,
Bob DeMarco 7:17
spread it thick.
Jim Person 7:20
All right. Well, we mentioned a very special guest interview that we always do on Sunday. And a fascinating interview bomb. I fought from a knife maker that started as a teenager. I didn't even know what I was doing in high school teenager but this guy started the knife business as a team.
Bob DeMarco 7:38
Yeah, and not just not just fussing around messing around in the basement with knives. He started a legit business at a very early age. I spoke with Nick Chuprin today of NCC knives. Fascinating guy. Great story. And, you know, for me inspirational. I'd love to hear how people take their passion and really, really turn it into their life and Nick most certainly did that but also his eye Meyer has knives so greatly I, I do not own one, but they are so beautiful and precise. And and his whole, his whole approach is is, is pretty interesting. And another thing is he's in New York City and you know knives in New York City are like oil and water. And so it's just very interesting to talk to someone who lives in a place that is so inhospitable to knives in general. And to hear how he has a flourishing business. They're pretty interesting.
Jim Person 8:31
And it's so expensive, just a to live there. And as he mentioned, they have you know, retail space or warehouse space or whatever in New York, you know, like, wow, I think
Bob DeMarco 8:40
one of the first questions I asked him is What's it like being a knife maker in New York and his answer is hilarious. That's right. Yeah, you'll
Jim Person 8:46
you'll hear that right up front. You'll hear that and we'll get into that right now here on the knife junkie podcast.
Announcer 8:52
Do you carry multiple knives then overthink which one to use when an actual cutting chore pops up? You're a Knife Junkie of the first order.
Bob DeMarco 9:00
Well I'm here with Nick Chuprin of NCC knives Nick, thanks for coming on The Knife Junkie podcast,
Nick Chuprin 9:05
no problem grateful.
Bob DeMarco 9:06
So NCC knives we were saying right before we started rolling your work first came onto my radar a couple years back when Dr. Frankie got a collaboration Knife of yours and then I started to see knives straight from your shop just you from I think birdshot IV was the first time I saw your knives and you are a New York City knife maker which which is a strange thing. Tell me what it's like to work and live in New York City but have your life be about knives.
Nick Chuprin 9:40
Gotcha. Two words. Illegal and expensive, I guess. Legal carry not actually make out here. Right. Um, like I said, living expensive. Being a knife maker in New York commercial warehouse spacing is very expensive. So expensive. In fact, I went from went full time at 17 years old. six or eight, six or seven years ago, I actually left New York. I came home from school one day, my first semester in college, I told my parents finishing the semester next week and I'm moving out. I ended up moving to New Jersey and ended up working alongside the guys over at New Jersey steel Baron. Right the warehouse space from them, even even ruminating on the owners of New Jersey steel Baron. They did that for about two years until I was able to afford living back in New York. That was back here and I've been over here about three years now was not much cheaper to have a warehouse and apartment out there. And just the shop out here.
Bob DeMarco 10:41
So what was it that brought you back to New York? Was it that it's home,
Nick Chuprin 10:44
a home and family, okay,
Bob DeMarco 10:46
it is a particularly stimulating environment. I lived there for about 12 years of my 30s and late 20s. And wow, what a place to be. But now Now that I look back on it, I was so cavalier about walking around with knives. I mean, I guess it was pre stop and frisk, but still, you know, it was it was kind of a sketchy thing to do but I was very very bold about it and and now I'm just glad I never got pinched you know?
Nick Chuprin 11:16
Yeah and I know exactly i mean the laws are a little nicer now that they suspended the gravity and I thought yeah, still kind of bullshit. Just because CAPTCHA aren't very well informed. They some of them still think this is actual law. It's not what they call the forefinger policy. And miliar with that a lot of a lot of people that I just know regularly that asked me They all think this is a law I don't understand how this came to be. They can't be longer than the four year the span of your four fingers side by side which makes no sense because everyone has different sorts size hands. I could carry on like this almost three and a half inches long or someone else carry an iPad three inches, where the actual loss four inches and now that they've expanded the gravity knife law, only thing that's really an issue. clips now, really so if it's if it's visible, it's it's a problem. It's invisible. go about your business, essentially. Yeah, but I still think it's sketchy just because there's like some weird law about it being scary, I guess, in different in different wording. The complex is like my eyes are compound round cantos, right probably be scary. That's a it's a weird one. I don't think they'll enforce that. But I still like almost people carry something like a Swiss Army knife, something gentle. Something that doesn't look too frightening something it's smaller. I still carry whenever I travel, pretty much work the car and thankfully I have friends of the police force and I'm a knife maker. Make sure I carry my business cards, right show show my wife my Instagram. It's at home. They'll get away with it.
Bob DeMarco 12:46
sounds legit. We've had Doug Ritter on the show. And he said he says just just keep it quiet and call me.
Nick Chuprin 12:53
Yeah, it's pretty much what he tells me.
Bob DeMarco 12:55
So you started making knives full time at seven You say? Yes. Wow. Okay, explain that describe your whole your whole coming of age as a knife maker at seven.
Nick Chuprin 13:09
So 30 sir earlier Actually, I started collecting knives at 13 and not like usually the story is someone's like, Oh, I saw this knife at a flea market now I went full custom. My firt my first knife was pretty much Oh no, my first knife was a Spyderco tenacious that I still had. The second knife was a sebenza no Mike so just kind of went boom. It would have been over like two weeks I bought a tenacious kind of into knives. Not really. But then someone told me about a custom knife show. I was mainly into handmade items. I like working with my hands as much as I can. And I went to that New York show had about 15 minutes there. My brother took me there and he wanted to leave as soon as I did one lap, and I said I'll be back here next year and the whole year I was deciding between sebenza and Strider got the next year got a sebenza actually one 300 RJ Martin onso I did really good to latos
Bob DeMarco 14:07
you're telling me you won all of those?
Nick Chuprin 14:09
Yeah, at the lotos. Now at that, at this time, I don't know how long you've been collecting for Bob. But a hinder was about $1,000 in a second there, right. So walked out of that show, ended up flipping all those knives, making about four grand in profit after song all those and that was the start of my shop. I went right into making I built the shop and in the basement of my apartment building, my landlord gave me essentially a four by four foot table. And everything that fit on that table was my shop. Aside from the compressor and sandblast cabinet that was off to the side. I was kind of messing around with fixed blades. I'll tell you in that year, I made maybe two fixed blades and ground about 300 I'd never really finished them I couldn't I couldn't bring myself to actually make handles and finish them until the grind was right. But during that time I was making bullet beats man I'm going to show those years but that was essentially what I that was my business plan is make these bullet beads back then beads were pretty hot meaning for lanyards for yes yeah, essentially they were clone eight 380 ACP and 45 ACP eventually I made nine millimeter and various brass copper titanium zirconium various materials and dealers a lot of them dealers are picking them up insanely while to honestly I was making about I made about five figures that year and just beads and I'll just show you where the bead market was back then. I 14 years old I was like wow this is amazing and I just kind of still there as a hobby and all throughout high school never really talked about it because you don't be that weird kid that that wood knives in high school especially in New York City. Yeah. But that all that money literally just helped me build my shop as I was learning the market and stayed very in touch with the market kind of as a somewhat of a dealer with a lot of shows staying on top of the forums trying to buy and resell I understood how to secondary and just put put that money back into building a shop slash collecting I was bill collector. I collected about six customers at a time whatever filter fill it in my case so anytime I wanted something else I would just sell something and put it back into the case
Bob DeMarco 16:11
That''s very disciplined of you sir I applaud you.
Nick Chuprin 16:14
That was just the way I was able to invest back in the shop I kept to money I want to be able to reinvest the shot, unfortunately, right before yes 16 for one full time I lost the shop that Hurricane Sandy. I'm right there in that little long partment center of Brooklyn. And my building is right on the coast. So I lost this tire shop. I was pretty distraught, let's say and I was okay. That's the end of that. I guess. I got lucky again at the New York customize show with a couple latos and got about two grand out I was like you know what, let's start to build again. And again, I wasn't making any money making eyes then I was just doing it for fun, and I wasn't really making the folder at that time I was about to start my first folder. The first folder was half done and Sandy destroyed it. I was making good money making the beats and thankfully that kept me encouraged to stay in this if I wasn't making beads or they weren't sewn, Sandy would have probably been the end of my knife career. Thankfully, the beads are keeping me motivated to do this and I still into collecting. I get into high school. I mean, I get out of high school at this time I'm already making folders. I think I brought my first folder to bleach my first blade show which was 2020 I guess that'll be 2014. And that was my first folder. My first hologram my first compound grind kind of went all out on it. Wow. And that was last year high school. So I was 2013 or 20. That's 2014 I guess. And I brought the blade show everyone love that. Every knife maker is like, Oh, this is great, but I could tell it just be nice to the kid. It's horrible. And that's why I got the college and the weekend. I really didn't like school. I was in there for engineering. Just wanted to work with my hands kind of talk to some engineer as well as in their doing apprenticeship. They realized that even mechanical engineering what I want them to be in for is the best job for the first 10 years. And I had no motivation to doing the best job. So I came home literally told my parents that day, I was like, Look, I have everything lined up. I'm going to try this for a year, I was ahead. My college credits were ahead of the year, the normal kids my age because of my high school credits. So I was going to do this for a year. They're, like hesitant, How's it look, I'm out next week. I have a plan I have. I had a pre order and I was in Alaska about six months. I was like, I'm gonna try this. And so for six years now, seven, six years now I'm still doing it with a 2000 square foot shop here in New York.
Bob DeMarco 18:37
That's amazing. So So describe the shop you're in now and and what you had to do to get to a point where you were able to move into a better space.
Nick Chuprin 18:47
Oh, as I mentioned, I went full time I had to leave New York, essentially, I had to in New York. It's pretty normal live at home flip until you're about 25 usually you don't move out until about two like my brothers was at home to us 27 because he was in college. It just it's not normal. Except I left that left in New Jersey. Thankfully, the nj steel bearing guys were nice enough to take me in there were pretty much had no life from 17 to 20. As I lived there Monday to Saturday, Monday to Friday, Monday to Saturday, I worked my ass off, made knives. And then on the weekends, I would come home and stare at the parents in New York. And that's pretty much when I went out. But for those three years, I dedicated my life to making sure that I could have built enough of a following and money to make sure this could be a viable career.
Bob DeMarco 19:33
Right. So you have a new shop. It's not new to you now, but it's
Nick Chuprin 19:37
about three, three, November was three years.
Bob DeMarco 19:41
So are you producing all of these knives on your own right now?
Nick Chuprin 19:45
No. So my father has been full time B for the last seven, eight months now. So it's it's been me and my father. Besides that I was always myself. I mean, he had to work like a Saturday once in a while if I needed like, if I was doing some job shop work and people aren't going to And I produce parts for other makers sometimes, okay, because I have CNC capabilities. And sometimes it'll be a lot of parts have to be sandblast that or something like that, that I just don't want to do and it doesn't have skilled labor. So my dad will come in every every couple Saturdays, something like that and take care of those kind of tasks. And he got fired by as much as six, seven months, eight months ago, about eight months ago, I think. And I was like, honestly, like, I'm really busy right now, can you afford to try this for a few months before you go for a new job? And he said, Yes, eight months, and we're still going,
Bob DeMarco 20:32
I gotta say, That's pretty amazing to be able to offer that to your father when you know he's been doing that for you your whole life, and you can turn around and offer him that that's pretty amazing.
Nick Chuprin 20:42
Well, I've had apprentices in the past. I'm not gonna name names. Unfortunately, when you teach someone how to do this in New York was a little easier, but the apprentices were out of Jersey. if they have any garage space at all, and they see me they see my market, they see my sales, they see how to do it and they see all these Are they kind of go off and do it themselves? Unfortunately, not something I was able to do. As I mentioned, that was a kid. commercial spaces insanely expensive. I probably have one of the most expensive shops in our entire community pay more for my shop than I do for my rent. And that's not cheap. They've it's just not easy to do in New York. And also, there's low skilled labor in New York. My dad was good. It was hands. I was like, honestly, let's go give it a try. And he's been so far so good. So one of the downfalls of working with your father, right,
Bob DeMarco 21:29
because you got to tell him what to do.
Nick Chuprin 21:32
Yeah, it's when you work with him, and then I live at home just because there's no just for ease since we carpool and Moe is at work, right? Plus, I live in a nice neighborhood in Brooklyn, but it's a series and moves so it's a weird dynamic is what me eight hours a day at the work 12 hours a day, depending on the day and then when we're free to home.
Unknown Speaker 21:51
Yeah, yeah,
Bob DeMarco 21:52
that the dynamic reverses, I would imagine. Hmm. So you said before that when you were first starting out and you were grinding You were making a bunch of fixed blades kind of working on getting your attributes as a grinder down. You said that you couldn't bring yourself to bring to put handles on to a, a blade that was in ground perfectly. Where do you think that instinct came from? Why not just get a knife out there that was imperfect.
Nick Chuprin 22:20
I just cut it out. I was a perfectionist. I am perfectionist. I'll make perfect knives. No, it does. But to the best of my capability. If I see a scratch or something that I could fix, I have to fix it as the right but there are flaws in the flaws are usually like it's the best of a grind that or it's the best I could finish that. Or if I know if I work if I work harder at the handstand that just gonna get worse because it's gonna be overworked and things like that. But if I made it to the best of my abilities, that that's what I try to do. At least in that case. It was to the best of my abilities, but not to what I consider sellable ability because I was trying to make some money to expand my Shopping I was like, well if I made this I would not buy this for $150 the going rate for a fixed weight of that style back then I was looking at it like that because I was a collector if I didn't think I would buy I couldn't sell it and same thing like I mentioned my first three folders I didn't ever have the first one the second third one I eventually did sell to like to consider friend collectors that are local that just wanted it but the first one still in my possession wasn't it's never gonna go anywhere forced to the second one did sell guy stop collecting and I don't I saw it on Arizona once Arizona customized that is and that's kind of gone again when it's one of those knives have kind of gone with a safe and never pop up again. Right?
Bob DeMarco 23:42
So if you were to describe your style or describe the things that you look to imbue your knives with, stylistically What are they
Nick Chuprin 23:53
modern, sharp, Art Deco. I guess. I don't really have organic designs and That's for a reason I don't I don't really like really curvy organic designs. I really like straight linear lines. That's why MK one is a straight line. There's a few arcs to it, but at the pivot tip too, but pivot, everything's a straight line, the knife opens 180 degrees. That was the point of that knife. I wanted it to be really straight. And my other designs that I do have are kind of like that. But that was that was that's just my design philosophy, the design philosophy, some people like really organic and really curvy and that's not my thing, same thing, but now that I do CNC the type of milling I do is a lot different. But when I did everything by hand, everything was chamfers I really like big chamfers and various styles and forms of it. I never really liked rounded like I like contours, but it wasn't really how can explain it It wasn't it was like an even contour. There's it wasn't like multifaceted contours and all sorts of directions. I just like variable uniformity and very linear, let's say,
Bob DeMarco 25:02
yeah, and and they all look very clean to me, you know, they got that clean. And then you look at the often your knives have tanto blades, beautifully ground, sledged, you know, multifaceted tanto blades. That looks like a very difficult thing to, to do. To me a tanto I mean, like, this is this is speaking as someone who's whose ground 20 some odd pieces of steel into knife like objects like it's very, very, very hard to do when you're not doing it every day. And then keep on the fact that that you are doing these incredibly complex grinds that are that are mirrored on both sides. What what are the challenges of that kind of production, especially when you're trying to move you know, make a number of them?
Nick Chuprin 25:50
Well, there's a lot of challenges to it. I take great pride in my tantos as you see most of my designs have been tantos the next three designs that I'm doing won't be just because To my father, the biggest bottleneck is me grinding blades. I take a lot of time to grind those pencils. Because I was I have a very specific checklist for them. I've seen many guys do similar tanto and as long as it looks like mine, but I've been making MK one for about eight years now. Back then no one made that knife. That was a reason I that's actually the reason I became a knife maker. I couldn't buy what I wanted. Oh really knives that wore that similar shape was Bob Lum tanto and by that Southern flipping tanto I did buy a les for his mini Abraham I wanted only two knives. I slow my collection. I see you thinking about it. Yeah, I'm trying to remember it. I had the mic is a one of two. So they're both one offs. And I got his books for another tanto and he calls me and he's like, Hey, man, I've already scrapped three blades. I can't replicate this. Do you want something else? So like I just grinded like a normal flat ground. 10 so I'm cool. I'm like a beginner knife maker. I get it. I get them. I didn't like it just because it was A ground like that saw that, unfortunately, but back then no one did it. I was one of the few that I've seen and john Barker was getting pretty hot at that time he did it, but I couldn't get one of those either because I wasn't gonna pay four grand and I wasn't having to have any luck with my latos now like, yeah, those my money if I want it, but I really would have wanted it if I want it to keep it. So, you know, we're trying to figure out myself now everyone in their mother does it as many makers. I always say if I became a make maker today, I would I mean, I wouldn't become a knife maker just because I could buy a Chinese robot that does a great
Bob DeMarco 27:32
huh? Well, okay, what you say now everybody does it. Do you mean everybody makes that the complex Hello, ground tanto harpoon like yes, like,
Nick Chuprin 27:41
Okay. There's a lot of great talent out there these days is a lot more information. And a lot more people jumping into this. They have prior talents.
Bob DeMarco 27:49
Interesting. You mean like, how half the people I seem to talk to were in the aerospace industry or worse?
Nick Chuprin 27:57
Yeah, usually. Then a guy came in That shoulder first knife was like, yeah, great treated cuts. Yeah, but it doesn't look great. Now those guys Oh, it's my second life. I'm like, Wow, that's really good.
Bob DeMarco 28:13
So you at some point, got a CNC machine, presumably that is to up your production, but also, what's the word I'm trying to?
Nick Chuprin 28:24
It was more of
Nick Chuprin 28:27
it would know it was more about career liability. Like I said, I was going to school for mechanical engineering. So I was already I had a mindset about making money and being is the viable, viable career. Also, I've always been a hustler and business minded I've been making money since I was 10 years old, the various business ventures. So in my head, I was like, Oh, this is great. I found a career that I can work on my hands as long as I make some money and obviously I'm surviving here in New York, so I'm making it work. Yeah. I got the CNC because I walked in at Brian Adel sharp by design. He Used to be a steel Baron all the time. And I got I became friends with him over the years and he invited me over to his shop and I go to his house, I check out the CNC check out his operation and his operations out of one car garage. Amazing. I'm used to working out of a shop fully equipped now that only works because he doesn't grind his own blades. He doesn't have a grinder, but he makes it work. Now like looking compared to my facility, like I said, I have 2000 square feet and I'm only using eight and eight to 900 square feet. It just the space that I have is equivalent I would have anywhere else I'd pay for eight or 900 square feet. So what I needed just at that place came up it was a mess. I just put work into it since I'm very handy. I built I fixed the roof that the plumbing that the electric built the walls. So I fixed it up and just the right makes sense to have the space as I need it. I grow. But I walked in there and I walked out and I'm like, yeah, this is possible in Jersey. So I was probably 19 years old. I've had the CNC for four and a half years. So yeah, I'd say 19 years old. I walked out of there I get in my car. It's about an hour drive. Home and it gets me thinking I was like, you know, I'm serious about making this a full time career that is the next step. I either I go CNC or I don't do this because I can't grind knives my whole life by hand 19 like I said, if I was ready to make this full time career, I dropped out of school, I had at least 40 years ahead of me doing this. And I had to figure it out. And I must think that every time I'm sick, I couldn't work. Every time I had back a guy I used to be very severely overweight at that time and I had chronic back problems so every time I go out, I couldn't work. I couldn't get paid. So sick you know what I have to decide to get a CNC how much is okay, I need 30 grand let's figure this out. How do I make this work? It's complex. You need grease for it. You need to take classes. I was like No, and I'm young. I've always taught myself how to do everything I do. Brian can help me a little bit along the way. I gave myself a year to get it. I spent about an hour to every night after work reading studying. Thankfully CNC is 80% in the program. So it's stuff that I could do without buying a machine Did all the programming up to the point where I had Mike designed the fixture designed, which is known as CAD CAD is the 3d modeling of the part cam is the G code that is generated from the model that the machine reads. When we say that again, I'm sorry. So CAD is the 3d modeling of the part. That is the statical 3d dimensional the physical item cam is what the machine reads. So you generate g code and the machine reads that and you use the model to generate the cam. So you're able to do all that without even owning a machine. That's the nice part about CNC. I tell everyone doesn't matter what machine you buy. 80% is in the computer, you can learn like Like for example, Rob, when he was looking into CNC I was teaching him and I was like looking looking to buy a machine you have to rush into this, get the program just sit there in your free time. Just mess around with it. By the time I had a machine I had a finished knife off that machine within a week because I had the fixtures design I had the knives design, I had the cam design. I had the tooling that I was going to use every Everything was pre planned out to get the thing going they want
Bob DeMarco 32:03
so did you see a change in your creative thinking or you're planning that you know, either your left side or the right side of your brain? Did you see some sort of a change in your thought process once you got the CNC I mean of course it changed your process. But I mean, did it change your creative thinking in any way definitely.
Nick Chuprin 32:19
As far as not design wise, not blade wise because I still hang around all my blades. As far as handle wise I get introduced the new world to me I was very good at manual machining being self taught. Back then a lot of guys knew me for designing fixtures I was very good at seeing apart designing a fixture to run manual now and CNC things don't pictures don't really matter. Just mount some screws and machine moves whichever way you want. But in manual machining fixtures are a big deal for repeatability and certain things. And I had that many makers, I think Rob and I flew out there and he's watching my fixture design process. I was just Really good at that. And that helped me transition to CNC. So I did a lot of unique stuff manual machining even prior to the CNC. But it did introduce a lot more things like in layers and certainly machining patterns that were really hard to do with manual machining. I was like, well, this is easier and repeatable. Since I don't really do the whole patterns, like a lot of guys do these days because I don't have to if I want to make it a triangle or a slot looking thing I can it's the same amount of work for the CNC.
Bob DeMarco 33:26
You've been doing this cool. I don't know. I've seen it a lot in on your Instagram page. But this sort of a grid pattern. It's like nurlan.
Nick Chuprin 33:34
I call it a prismatic grid because it tapers out the dive. Yes, yes. And I should do a similar pattern manually. But it was even it was more of instead of a frag pattern, there was a diamond frag, and this way I could, which would win insanely hard to do manually. But with the CNC, I could tell it to array out and it's in a specific degree and that's why it gets bigger and spread out. It was a similar pattern. So I started messing with finishes and I did I finished that many units ways because it allows for a lot of facets for different for different sanding and tumbling processes,
Bob DeMarco 34:05
right? And it seems like well now having the capability of the CNC you're able to get that pattern and it it actually enhanced your creativity because that pattern is really cool the way it the way it arrays out and your eye is searching for regularity but it doesn't find any. But you know, it's got to feel good in the hand. You know, and it's got a you know, it looks good, it feels good and it's a maybe it's a feature you wouldn't have before you had this yeah ability back then I used to do more. I did a lot of milled mill milling on handles, but I was built for my various sculpted chamfers a lot of guys do 45 degree standard chamfers now it's a little different. But if you would a best way to describe it. It was a style that I inherited from Jeff tuff dubs.
Nick Chuprin 34:51
I watched him a modern MP one use that you see, yes, the gen four or five, but it's very close to the gen two and the Jeff I mean, the gen two was, because of Jeff Lavelle, I went over to his shop and he reshaped them k one. And that's what it looks more similar to my original K. One is actually like I said that it's organic stuff, but it was a little bit more organic. He made it more linear and sharp. And that kind of went off from there. Now like I said, I'm one Gen five or so but back then it's closer with the gen two would have been the only downside the CNC is very consistent, but it's very expensive and painstaking to make changes. Back then my knives were more unique and different. And every time I sculpted them nowadays, I still have a lot of patterns considering compared to other CNC makers for design, but it's not as many as I'd like just because of complications when doing orders. Well, are the are the errors fewer and further between, though? I mean, they're they're harder to fix, but do they happen less often? No, they haven't more often. So usually, when you do things by hand, you would have one error one time and you learn the next time. Unfortunately with CNC the machines only as smart as the human If I miss a.or a line somewhere I could pick up 40 cents a handles before I realize thousands of dollars which may or may not have done in the past. Right, right. Actually, I was the first patch batch ever did I've spent all the money in the CNC and I was like, Okay, I'm almost broken. Make sure these knives work. And I made three that work great. And then I missed the.or a line somewhere, which means a lot because that could mean an insurer dow I don't remember exactly what the issue was or something with the barren counter bores, and I messed up 40 sets of knives. So after spending all that money, being 918 years old, 19 years old, right here on the CNC still have bills to come and I messed up 40 knives after paying for titanium, steel, he tree waterjet everything. And then I have to start over and I was like, well there goes all my savings. And I pretty much started with nothing, no money in the bank. The CNC just sitting there. I was like, Whoa, I run the CNC like as if I'm a manual machine and it's mostly CNC knives one by one for about Three months there until I really figured out every error and meaningful lesson. Yeah, it was it was that thing. It's like oh, that nice, easier to make and fix. I was like, honestly not really want just as soon as I figured out every issue and every problem and how to counteract it from being a Manulife maker, I get this curveball and I go CNC. It's I felt like a novice again. It is if I restarted some scratch, the issues were different. The fixes were different. It was an entirely different ballgame. It's everyone's like, oh, CNC is easy. I'm like, it's not it's different game. It's actually harder to be a CNC knife maker than a CNC machine. Hello Fresh, I'd say if you have no knowledge of it than the manual maker, because yeah, if I have a new designer, I'll make a new manual one tomorrow. If I got a new design, I can't make it on the CNC for three months. They'll have everything figured out because you have to code it. Yeah, right. Yeah, to print the code it and it for example for me to go make a knife, a brand new design, two sheets of titanium and a piece of steel. I'll have it in there too manually done and If it works, it works. If it doesn't work, it doesn't like for me to make a knife without fixtures on the CNC, or do it with fixture just to get it going, that first item cost me three grand my cost just to make all the fixtures and everything, you can't just slap a piece on there. So it's an entirely different ballgame.
Bob DeMarco 38:16
I want to back up to when you went to kind of the beginning when you moved from fixed blades to folders, because this is kind of a similar question as to go into the CNC CNC machine. You're going from a fixed blade, which is a simple concept. You know, I'm not saying it's simple or easy to make a good fixed blade, but it's a simple concept. And then you're moving to something that's a folder that has a that is not a simple concept. It has mechanics and it has, you know, it has areas where you have to be so precise. So what was that transition like going from something fixed and inert to something that is mechanical and and always dynamic?
Nick Chuprin 38:57
I'm easier actually say I'm very good with mechanics I've actually never sold a fixed blade when I started I didn't sell fixed blade until about two years ago when I was in kitchen knives the focus of the fixed laser hobbies I was realizing like there's no money in this and for me like I said it's a hobby I'm not all about the money but again I've been full time for six years or so and maker for 10 I don't want to sound arrogant but it's a business I have to make money. Yeah, and like said I was always looking for long term viable long term viability and I was like, Well, I have to make folders anything with the CNC I walk into the shop I walk doesn't have to be a staff to get a CNC and I mentioned I got the CNC in about nine months studying and teaching myself over nine months an hour to a night goal was a year so I ended up getting early because I found a deal but just go back to the saying I just didn't the fixed wages Didn't they didn't sell out right away. Let's say I knew I wasn't gonna be a sell maker right away but I didn't really back then I didn't know any sell up fixed weight makers just didn't really exist. They didn't have the same clientele the same market. Sounds like you know what I got to figure out the solar thing. Plus, it seemed more interesting to me. The full x rays were kind of boring and I hated working with codecs.
Bob DeMarco 40:08
Fixed fixed blades. I mean, I love I love all knives, but really a folder. folding knives seems like a great place to go because everyone kept Well, not everyone carries them, but you can carry them all the time. Whereas, you know, I'd love to be a big old nerd and walk around with my fixed blades and my swords on me all the time. But, you know, can't do that. But I can walk around with a pretty, pretty sweet knife in my pocket. So, yeah, it seems like that is the business savvy decision. You mentioned before Rob Carter. I think Rob Carter, you mentioned rob a couple times. I'm assuming Carter and Jeff Glover, who are some of your mentors. I'm assuming they are. But did you have mentors or people who influenced you as you were deciding to shift your life in this direction?
Nick Chuprin 40:57
Honestly, I'd also like to say I don't really had a mentor. I just kind of had people that were there. Well, Jeff law without just in the beginning, I kind of just knew Jeff because of the shows he was pretty close. He helped me with that first design. And me and Rob, that was like a week into it that became more of a mutual relationship than this. He's a mentor to me. My relationship with Rob started on us son, I asked for a question about defense when I was starting to folder venture. He just dropped off his number He's like, call me seven hours later on a phone call. We talked the whole time the mind you this is a grown man and I was like 14 years old and he gave me the time of day to answer all my questions. So as I got more into knife making, eventually Like I said, I was the fixturing design and mechanical part of milling kind of just came to me. And he was just getting into machining himself. He was he was a lawmaker for a long time, but he was classically trained by his father and grandfather were legends. Their processes were very different. So as soon as I got really into machining, that became more of a mutual relationship. He, he taught me kind of the basics of how to get going. And I told him how to modernize his knives and modernize his processes. If you could, there was a day where it all changed my eyes and his he would notice the first time I flew to Texas in December of whatever year but whenever we did the Mk 16 project, is I showed him all my machining tricks and he showed me all his whole tricks mainly, why is this knife sticky? How to fix it? Why is there a lock crop, how to fix it, stuff like that, and that that week changed both of our careers for the better, and that they just screwed. I was definitely over six years ago, about seven years ago, I think. Yeah, I was about seven years ago. Now it's kind of the same thing too. I call them everything I do is really quick. I don't not really I don't like to drag things out. I call them how's it go? Can I come down next week? is serious. I'm like, Yeah, I came home my parents again. I was like, Okay, I'm playing in Texas for a week or two next week. And I was in Texas A week later. Then I was culture shock because he woods.
Bob DeMarco 42:57
This led to the Mk 16 This trip.
Nick Chuprin 43:00
That's Yeah, that was just because I have an MK one and he has an F 16. Right. And they were very similar design eyes already. And we're like, oh, just more fun. Let's take my more of my blade style and take your handle and mix them
Bob DeMarco 43:13
that that knife if I'm correct has such a cool feature on the spine of the blade. It's got a harpoon, but then it's got between the harpoon and the jumping, it's got like this semi circular dip
Nick Chuprin 43:24
into the top and that is the newer ones. So mK 16 was essentially it had jimping we only made like nine of those, this was like seven years ago. It was longer so it was off of my MK one s mean L which only made about six of those two, so three and three quarter version was more of my blade. Because the ratio is that his blade were different. And it was literally a half and half more of mine escape handle is F 16. If you could picture it was too It's too big choices, I would say are two big arcs. And but it was a little bit more organic and then what so I kind of do Essentially, he sent me his file, and I mashed mind into it and finished the design. That's how most of our co labs work is, a lot of our design aesthetics are similar. So he would send me his file, and I would take my knife that looks similar to it, and I would do all the morphing and mashing together. Same, that's what the new vbm was. He sent me his knife and I completely redesigned my aesthetics rescaled it redesigned my like the first half of the screw going through the clip and being the one screw construction. The fuller the way the holes done, that was my static to it. We didn't make many of those, the one you're mentioning is the recent colab we did which was just my MK one. And I just kind of took a little arc at the back of the blade. But essentially that was not a design cool that that was more he flew down here we made those together. Oh, because it was a very short notice trip that that trip was all decided within the month is you know what, we don't have time to make more vbm so just make this MK one RC thing. So that wasn't really a design thing that was just come down. we'll grind these and make these together.
Bob DeMarco 44:59
So Do you have other collaborative relationships like that is is that a difficult and rare kind of thing to maintain?
Nick Chuprin 45:06
They were easier to make when I was a manual knife maker. Being a CNC knife maker doing new designs, like I said, I think a lot of r&d and that was the reason we did MK one RC is because it was all the same pictures the blade was instead of a Japanese tanto shape, it was American tanto because, and a little soup thing at the back the handle one to one my meal patterns one to one, the blade is the only thing that really changed that at knife. We made about 40 of those, but that was the point of it. It was very short notice. We We We lost money on the BBM project, even though became a success. People made more money on that project than we did. So the point of RCS is second and third trip was to try a new process and nail it down. The second trip was great. How's the RC trip the third trip we're supposed to make BBs and should happen. I had some issues in life and I was gone so you don't have time to redesign the dBm from the new process and you'll find down three weeks. There's no time for water jet heat treat logistic RCS right now, again, and that's what we did and the new product the third time he was he was the finalized version of the process. And it was great. We three weeks from May 29 set lots of detail and 17 more. And it was it was profitable trip. He was happy. I was happy. We're like, cool. We're doing this again. He should he was supposed to come back here in July ish to do VMs. Again, we haven't mentioned that yet, but it's not happening. So I mentioned the good Okay, so the whole virus situation, right. We are still planning on doing them this year, which kind of figure out what the virus situation how to get this to work, trying to figure out how to do it remotely or we're still trying to figure out the virus has managed to cancel so far. The other cool labs I've done kind of here, they're with john gray. He's a local maker than about five where I make him give him a knife that's lochia D temping and machine it all out right on machine the bat like the machine in the bevels on the handles, a lot of the contours just just a wreck essentially, with conda with counterbore says with the screws In, I said a lock in detail, I have a very unique action. very snappy. I don't like what I what I call Olympic action. I have to when I speak, Rob, if you flip the knife breaks the detail, it's gonna open, straight and a half open. My knives never usually half open at least how I opened them. Just because flipping a knife is an art, I'd say it does take some muscle memory to figure it out. For example, my dad can flip mine I was open for about three months, I realized that like, it's not, it's not something everyone could do off the bat. There's kind of a technique to it. I'd say. It's something I used to notice that shows when I Exhibit A lot of guys pick up a knife and like don't open it correctly. You know what I mean?
Bob DeMarco 47:40
Yeah, yeah. Well, I would imagine if you if you're used to, you know, if you're someone who opens a lot of frame locks, you're you'll probably do all right, picking up your knife because you kind of know not to grip it too tight over the lock and all that kind of stuff.
Nick Chuprin 47:54
Yeah, it's usually the lock thing and also the angle that they flip them at. Even me as a customer. maker, I'll pick up someone's knife, I might fail football correctly the first time, but you'll get a second or third. Sometimes, like my knife has what they call a trigger flip. It's straight up and down. That's because my Lippert, and I could do that mathematically, I know how my knives are gonna flip by the mathematics. I like layup design. If it's above, essentially, if the flipper tab is above the pivot, it's going to be a pull a trigger flip. So straight down, that flips. If the knife is at the center of the pivot, or under the pivot, it's going to be within like there's not really any force, I'm actually just pushing it in towards the pivot like a 45 degree push inwards, right? My eyes won't flip that way that pivots a little too high and it detects a little too strong. It has to be a trigger pole. But that's just the way it's designed. I have different designs that are triggered, I mean, 45 degree and we're pushes but as far as MK one goes, it's a trigger pole. That's the
Bob DeMarco 48:53
that's the action you're looking for.
Nick Chuprin 48:54
Yeah, it takes more leverage to flip them. It's a little harder. It's not for everyone. I've had knives before where I've shipped them. And guys, like I can't flip this open. I'm like, Oh, I can make them a detail a little lighter for you but it's not my life might not be for you. This is honestly I don't make enough for everyone I was inspired for the 10th saw for RJ Martin's dimes and McManus mcginnises knives. Those are the two knives I studied when developing my data.
Bob DeMarco 49:17
I have never handled either, unfortunately, but I take it to have the hard crisp defense that you can't miss flip.
Nick Chuprin 49:25
Essentially, yeah. And I was the knives that I collect. I said I started making knives because I couldn't buy the knives that I wanted to. And same thing with the action. There was knives like that. And those actions I did own RJ did only guinnesses when I collected that was easier to find more than the grind was but again, I make what I like I don't make an eye for everyone. I don't think anyone makes life for everyone unless the production knife.
Bob DeMarco 49:48
Do you carry one of your own that?
Nick Chuprin 49:50
Yes, it's one that's very it's not perfect. It was the third knife I made. I need to really make myself a nice one. It's very off center. It's essentially not like a hair off center. We're getting Like it's off center, essentially you can't fit up. It's not growing on the side of the frame. But I can't put a paper between it's, it's tight.
Bob DeMarco 50:07
I asked. I asked Jeff Blauvelt the same question. You carry your own knife. He's like, do you carry your paycheck around with you all day all week? Like, I'm good. I'll probably start saying that was a good one interesting point, man. Because well you figure if it's if it's good enough to sell you got to sell it. Except if it's not good enough to sell well, you may as well carry it around with you so you can get get the skinny on it and know what to fix in the future. You know
Nick Chuprin 50:30
why every time I see Jeff usually carries on once in a while for like a week but then he always sells it, which I used to do back in the day to nowadays I'm more I'm not as connected to the knives I made these this. It's a paycheck. It's a knife. Most of them okay, one design made it so long. It's kind of I'm really bored over it. I was supposed to stop being me made like two years ago, but a few complications just kind of kept bringing it back. You said you're less attached attached to your knives, then you want to work. Is that because you've made so many of them? Or is that because your process has changed? And, and it's part machine part handmade. Do you think that has detached you at all? No, I actually am more fond of CNC made knives nowadays than custom knives for one reason. A custom knife you can't always tell where knife or mic maker messed up and how much attention he takes to the knife every it's very easy to round over a sharp corner you just take it's a scotch Brite wheel. But in the CNC and I could always tell how diligent a maker is about setting up the CNC. It's very easy to tell a little five chamfer that just slid right the corner is was set up and tolerance and spec by the evenness of the chamfer you're not going to tell them eviction for but on the inside of the handles that have a 510 chamfer you if you know you're looking for you always tell how diligent the maker is about setting them up. Now mine aren't always perfect every time either. Like I said they're not perfect. It's not something a normal collector would notice. But there's enough of a perfect area where you could tell where it's like this guy just didn't know what to look for or just doesn't care or Is machine dependent also depends on the machine he's using, but just how careful he is what is fixture. For example, I always have to be diligent that my fixture has a four part stack for example from the table to the actual part. There's a master pallet and there's the pallet sub pallet and there's the actual part of the pallet for the handle. And then there's the handle. If there's a chip or a burr anywhere in between those parts, those little tiny champers will be off if it's a little chip or if there's a scratch because the scratch will be raised and won't sit perfectly. You will never notice that anything big but such a fine little chamfer just to D burst something you'll see it it's like the the pee in the princess or that you know the princess who sleeps on all the mattresses but can still feel that tiny pee underneath the bottom one you have to go out to jail diligence, make sure you sanded everything flush make sure he inspected everything. Make sure you blew it all off. And there's guys who just kind of slap it on there and let it rip and nothing wrong with those either it just when I look at it, I could always tell when something's wrong. Like Brian Liddell used to call me out on that all the time when I first started. He's like 3d machining something it'll be like a missing line of code or like I said a bar or something where something's not exactly level headed like what's that extra line there with? Why is this one line squiggly or something down like you suck used to call them out like
Bob DeMarco 53:13
so would you ever send when your designs to a react or best tech one of those companies or is that kind of a moot point?
Nick Chuprin 53:23
I thought about it I was supposed to work with react for a couple projects never really happened. I have a very sour relationship with Chinese in the sense of my dad had Chinese manufacturing for a long time. And he was fucked over by them a few times. And honestly, I've been taught by the Chinese a few times. So every time I try to I kinda get hesitant around the project. Now like I said, many people have great success with a promise I tried to do a pre order with them and shit without like the Mk 16. We did a pre order for that. Back in the day that was that we made like I said six or nine customs but then we were For the production, and I'm taking out pre orders and something happened along the way. They took on someone else's bigger project, and they ghosted me. And I had to do refunds for people. Oh, that's Terry, I was never fun. I had to do 75 refunds that ruin my paypal credit history. Because I go through about 100 transactions a year, which it's, it's a little bit for PayPal, each one's a folder value. So it's a store of value that was back then at least, but they don't for the loans and stuff like that. They don't look at it, they look at ratios. And that messed up my credit history for a while it just put a salty taste in my mouth. And as far as design, there's not really a point if I was a manual maker or something like that, it would have been more of a reason to do so. But if I really wanted to simplify design and make 200 of them, I can I could always know my bevels on the CNC and like I could do that. There's no reason to give it to them, and then just hurt my market no matter what anyone says the moment maker does a project which is There's secondary drops their market drops. And I don't make a knife week like most makers, do. I make a knife a day, sometimes more, sometimes less. Sometimes I don't make a knife for a single month because I'm doing r&d. And sometimes I'll make 40 a month, just the quantities I could put out. Or if I would want to, I have never have put out crazy production quantities, at least with the custom folders, I have a different products just doesn't seem the risk versus the reward. I mean, the reward versus the outcome. Yeah, it's fat, a lot of money in my pocket at the end of the project for little labor. But what's the long term effects of it is what I was looking at. We were supposed to do a VM with China for whatever. Yeah, and me and Rob, I want them to do I want them to pay for it out of pocket. It's a lot of money out of pocket instead of doing pre orders because I don't want to do it like last time, right? And every time I'm about to do it, I'd have to spend the money or didn't have the full out of pocket. And I always go back to thinking like oh, Rob, do we want to do this or Let's just make it simpler or do it some way and let's just do it ourselves or we could make a third as many customers and make the same amount of money just fly down whatever. We want to really hurt that market pbms have a good secondary why heard?
Bob DeMarco 56:11
But that really is the beauty of having your own means of production right in your right in your own shop. I mean, you don't you don't have to rely on anyone else. It's nice to know that there are those OEMs out there and they're making incredible work there are also American OEMs you know, for those for those who need them, but it doesn't sound like you need it. So I mean, that's the thing I thought
Nick Chuprin 56:31
about it. So yeah, let's go. There was points from IKEA. I really liked the X that extra 10s of thousands you get really it's not quick takes half a year, whatever. But the money comes in within a week. Yeah. Once everything's said and done, I thought about it. That's easy money. I kind of need the money right now. I want to buy another CNC and it's always like, Hey, what's the long term effects of it? Everyone's market always drops. I've never seen that fix anyone's market. It's always I've never really seen it be better for the actual custom end of the business.
Bob DeMarco 56:59
I can see it dilute the waters, right? I mean,
Nick Chuprin 57:01
Mm hmm. And like I said, I'm in it for 40 years at least, just built a name in America. I'm actually working with another knife maker on an American production company. I'm talking about two to $300 knives the actual true production. Wow, maybe a year out half a year out. Well, give us a call.
Bob DeMarco 57:18
Give us a call. What you know, when you're ready to announce it, I'd love to know
Unknown Speaker 57:21
we're working on it. We're supposed to have prototypes at Blade Show. We've kind of put it on the back burner a little bit to make sure our own things are going but it's gonna be automatics. It's not gonna be frame locks. It's gonna be I could actually now it's at me and Matt. Ready? Ready? So it's me and Mac this skin?
Bob DeMarco 57:35
Oh, okay, cool.
Nick Chuprin 57:36
So yeah, we're gonna be calling it syndicate knives or syndicate blades. It's essentially gonna be like a separate like pro tech level and more like production. price points. 200 bucks. 300 bucks for high end, ones, maybe less for certain ones and semi custom versions. Not in the grind as blades. We will have verses that are hand ground crying by others others but I will be doing all the manufacturers In the assembly and house prototypes, I'll be announcing now that like, because of the virus, I've been working my ass off, they shut down in New York. Yeah. So I was given the approval to still work. But I made enough inventory. And thankfully, the community is great. And clients are great. And I was really stressed out last week while I was finishing up product, but sales haven't really stiff, slow down, definitely. But I still say I'm selling about 75% of what I used to week. I'm extremely grateful for that. And so that like I said, I made right before this happened, I'll probably working on my biggest batch of my career, because I didn't like I said, sometimes you have a month where you make a lot sometimes you don't like I didn't make a single knife in February, but it translated to the mountains that finished in March. Right. And so I was like, Oh, this is a great time to have a giant inventory. I guess. It's crashing.
Bob DeMarco 58:49
Yeah, yeah, you plan that well, man. So yeah, before we wrap up, I want to ask you about the bleed ology podcast, how long you've been doing that and tell me a little bit about it and what you get out of it.
Unknown Speaker 59:00
Well for me I was never maker who's really public with my personality. I'm very I'm not an odd person I'm an odd person for my generation I say not very social publicly I love to social person but I'm not I don't really have social media for my personal life I have one social media for my personal life to get just stay in contact my friends. I'm glad to say it but I just don't like I'd like I'm also I like to be out in person I hate when I'm out with my friends at a dinner table or on their phones. It's just oh god, it's not my not my thing. Like I said, I'm till I was about say 24 so I'm used to saying 20 423 it's just not how I am and so you never really seem to talk about myself, either. I've never really post pictures of myself my Instagram I was like, No what? Ever since my dad started working with me my output has gone up three times actually. Usually to work to corporate workers actually makes three competent workers because I could stay busy what what I'm better at he stays busy. Well, he's better at battery produces. We feel each other. Sure. comics, or essentially he fills in my procrastination is that I don't want to do he takes care of a at that point no further step into marketing I have to start talking about myself more showing who I am with the businesses like stuff like that I approached Jeremiah is a friend of mine for a couple years. He's one of the owners a PDK. Vegas. I was like, do you want because he has a media background? I was like, do you want to start a podcast This is mainly now there's a bunch of podcasts. There wasn't many out there and I wasn't in it for the fame glory and we don't run it too crazy because I'm busy maker and he hadn't said when he can when he can and he does. We don't do the whole Reddit and really marketing it really really hard. Because we don't talk about basic EDC stuff every day. Mainly there's three of us it's me, Jeremiah and Elijah Asham. So we have three very unique perspectives on the industry being Nizami me him being the dealer meeting the maker and I should meet the design We don't like Like I said, we don't talk about what's going on community ever get at the beginning we kind of tried and we also we do a lot of shows we did 11 shows together last year we go through them all together. We try to talk about the show before and after, but always kind of became the same old thing. Oh, Nick's working his ass off. He's not sleeping, Jeremiah's got to go buy a bunch of stuff. Like just like, cool. I'll see you guys there. And the same thing when we got back was always kind of the same thing. So we don't really do those anymore. Mainly, we just concentrate on interviewing knife makers. Our episodes are a lot longer than yours. About usually an hour and a half to two hours, sometimes three, depending someone like makers we have interviewed or 40 years in the business. Yeah. And we all Jeremiah's more in touch with the old school makers. I'm more in touch with the new school makers. So we kind of try to alternate every other episode. It's more about recording the history and just getting in for my benefit. It was important history kind of gets me out of the shops to talk at my house and still consider business
Bob DeMarco 1:02:00
Just get my voice out there people hear me talk more and so on. It's fun. Yeah, it's not it's not profitable at all. Obviously it actually cost us like $400 last week to set up the websites and cast all that value. We're gonna make that money back off of it. It just it just fun. Yeah, and it's a great way to catalog your career and and, you know, you mentioned how you have three very different perspectives. That makes for an interesting interview because you know, the three of you are all with your questions coming at the interviewee from a different perspective, I think that's pretty cool.
Nick Chuprin 1:02:33
And also, same thing for me. I said, I want to get my like, my personality out there. If people don't know me, Sydney for a lot of these makers, like if you notice we interviewed a lot of old school makers. So guys, you guys don't even know who they are like Reese Weiland, for example, two weeks ago, I was a four and a half hour episode that we had to break up in two parts. And that was after Jim I edited a lot of it because he has so much history in his in his knife making career that we get we get sued for A lot of it because you talk about things that he's not allowed to Hmm, just because he's like, I don't give a shit anymore happened, whatever I'm like, I'll leave that out. But he has a really rich history to where I didn't even know that he invented the button lock automatic for example. Oh, wow, he did that. Or it wasn't the but it was the pretty much the button lock he invented. He talks about how he was the biggest regret in life was not a bad thing that system because he would have made millions by now many companies use it.
Bob DeMarco 1:03:26
Yeah. So what is the future of NCC knives.
Nick Chuprin 1:03:31
Right now I'm trying to buy another CNC because I got to once you get a new employee, it takes a little bit to figure it out. But I'm kind of at that point now to where I'm manufacturing more knives leaving my shop and the machines actually cutting. So my dad gets dead points where he's like waiting on parts for me. So now the next goal is to get another machine so that way I could meet up meet the men make enough parts to where he's always he's always employed but there's some times where he I pay him to do nothing. Sweep the shop clean because I'm like I mean like I'll have four He sets the handles but then I don't the machine the blades are still machining so they're there to before I have blades for these handles for you and then even then it's like he'll start assembling like 10 knives with one Backspacer I'm like I need a couple more days before Exacto knives. So it's kinda it's the flow isn't perfect, but I did the math and you know linear CNC Well, I was trying to get one within my blade show essentially what the market better off stockpiling my savings a little bit. Right writing this out see how the economy goes before buying a machine and then the syndicate thing that's going to be a big part of my career that's we're trying to start production company that's not a side business syndicate. I mean,
Bob DeMarco 1:04:39
that rear What can you give me the full name of that again,
Nick Chuprin 1:04:42
syndicate blades, syndicate blade, I want them to be syndicate blade works but I got overruled.
Bob DeMarco 1:04:48
That that'll be something that'll be cool because because it sounds like you're making it affordable. But obviously you got two marquee makers attached. I mean, that's not not just attached to marquee makers. Collaborating for affordable knives i think i think you guys just knock it out of the park. Yeah,
Nick Chuprin 1:05:06
I have the manufacturing means and the will young I work stupid hours as is right? What's an extra couple hours over 24 and Matt has the years of knowledge and experience. So it's kind of a perfect match. Something I was kind of joking around with him about. He's like, I'm ready. I'm like, What do you mean? So I'm ready. Let's do it. Okay, spirit FM, kind of been messing around with it for about three months. And I made a prototype. I haven't really showed the prototype yet. It's MK one micro. That's how custom but it's what I used as the platform to figure out the automatic and we already have springs made custom springs custom buttons, and I'll say the springs we've made it better than anyone else. Any other company tested all of them and Matt spent some Matt that's Matt spent some time developing a better spring.
Bob DeMarco 1:05:54
I can't wait. I can't wait to check it out. I'm on. I'm on an automatic tear even though I can't Carry them in my state I don't carry
Nick Chuprin 1:06:01
anything okay. Jeremiah chose that whole life like, like side of knives to me I never caught them now I actually the only collection I have now are automatics yeah I heard cortex rotex there's fun.
Bob DeMarco 1:06:12
Yeah they are addicting I have a I have a dual action Lightfoot micro micro tech from 2004 that I got recently that is so cool anyways is please tell everybody Nick how they can get in touch with you how they can follow you and and where how they can actually get their hands on your knives.
Nick Chuprin 1:06:30
So you could find me NCC knives Instagram My website is active unlike most knife makers actually keep it up day and run it except the random portions I now that I'm at home I'm actually gonna build a new website, updated a bit the shop does work. NCC knives at Yahoo comm We're at gmail.com or the contact the best way to contact me those the contact page on my website is that if you've ever ordered anything from me or will order anything from me, it links it all together.
Bob DeMarco 1:06:59
Well Well Nick, thank you so much for coming on The Knife Junkie podcast, it was great to talk to you and get to know you a little bit and find out about your knives. And really what an interesting story you have. You're a young man you've done so much so far in this in this field we're all obsessed with or at least most of us and you know my hat's off to you. I can't wait to see what you come up with and I can't wait to check out syndicate blades in the future. Thanks again for coming on.
Nick Chuprin 1:07:27
Thank you. I just want to mention one more thing I forgot. I'll be doing right now as you mention where to get my knives I usually do orders only once a while every couple knives I do something for sale. But I'm going to be doing a pre order right now and those MK one micros that I mentioned. Right now that I'm home trying to figure out all the options and get it going.
Bob DeMarco 1:07:46
Nice. Well you heard it people get on that. You said mini or micro
Nick Chuprin 1:07:52
micro so that's the K one same knife but it's two and a half inch long plates tiny one.
Bob DeMarco 1:07:57
Okay, cool. So So get on that pre order now. While while while Nick is at home and working that all out, get on it early and often. Alright Nick, thank you so much.
Nick Chuprin 1:08:08
Take care. Thank you Bob and Jim. I really enjoyed it you guys tight ship here.
Bob DeMarco 1:08:13
Thank you sir. Take care.
Announcer 1:08:16
Have a question or maybe you just have a comment. Give us a call at 724-466-4487 we'll answer your question on an upcoming episode of The Knife Junkie podcast that number again 724-466-4487
Jim Person 1:08:32
All right, Bob Nick Chuprin a New York City knife maker you can find him at NCC knives.com I always try to ask you your key takeaway or interesting thought from the interview
Bob DeMarco 1:08:44
to me as usual was very interesting to hear about his process and to hear about how he actually constructed his business and and the different sacrifices he made along the way at a very young age knowing what he wanted to do and and I find that all very, you know, very Interesting and leads to these amazing knives. But the thing I keep thinking about is I, I love when people surprise me. And it's very easy for me to lump entire generations worth of people into one category. But I love to hear someone young in that, you know, kids today, he's a kid today. And he's killing it. He is, you know, he's got a thriving company. He is really excellent at making knives, he can support the folks around him with his business. So an inspirational story all around him. And I love to hear that it's coming from someone so young, who, who, frankly, it's easy to dismiss the young when you get a little bit older and crotchety and these young whippersnappers
Unknown Speaker 1:09:41
and and he's just, you know, he's, he's really
Bob DeMarco 1:09:44
shown a good face for his generation
Jim Person 1:09:46
well, and to rebuild his business or his shop because, you know, the first shop he built got taken out by Hurricane Sandy. And I was like, you know, just to have that determination at that age to do it again, and keep going. like wow
Bob DeMarco 1:10:00
yeah and once you once you do something like that at an early age it's kind of like taking care of your exercise in the morning the rest of the day you know you've got well he's faced some some big things as a as a small business owner. He's overcome
Jim Person 1:10:13
exercise in the morning maybe that's my problem. Or maybe I just don't like exercise. That's the problem. Oh, yeah, yeah, that narrows it down. All right, that's gonna wrap it up for The Knife Junkie podcast but again, a reminder please join Bob on The Knife Junkie. youtube channel, this coming Saturday, that's April 18. At noon, The Knife Junkie. COMM slash YouTube. It's going to be a great several hours Saturday afternoon live knife Hangout, and I know I can't wait and we can't wait for you to join us.
Bob DeMarco 1:10:43
And I'm pretty sure you're not going to be going anywhere or doing anything at that point. So you might be doing something but you can still listen, you can still tune in right?
Jim Person 1:10:51
Absolutely. Absolutely. Not till May probably. Maybe even June Who knows? The knifejunkie.com slash YouTube. Make your plans to join us Saturday April 18 at noon and if you want to listen to this podcast future podcast past episodes you can also go to The Knife Junkie calm and you'll find all the podcast episodes listed right there so for Bob The Knife Junkie DeMarco I'm Jim the knife newbie person thank you so much for joining us on the knife junkie podcast
Announcer 1:11:19
thanks for listening to the Knife Junkie podcast If you enjoyed the show, please rate and review it review the podcast comm for show notes for today's episode additional resources and to listen to past episodes visit our website The Knife Junkie calm you can also watch our latest videos on YouTube at The Knife Junkie calm slash YouTube check out some great night photos on The Knife Junkie calm slash Instagram and join our Facebook group but The Knife Junkie calm slash Facebook and if you have a question or comment, email them to Bob at The Knife Junkie calm or call our 24 seven listener line at 724-466-4487 and you may hear your comment or question answered on an upcoming episode of the night. junkie podcast.
Past Episodes
Catch up on past episodes of The Knife Junkie Podcast.
Subscribe to the podcast in your favorite podcast player or by RSS so you automatically receive each new episode.
Join The Knife Junkie community and we’ll email you when a new episode comes out so you don’t miss anything.
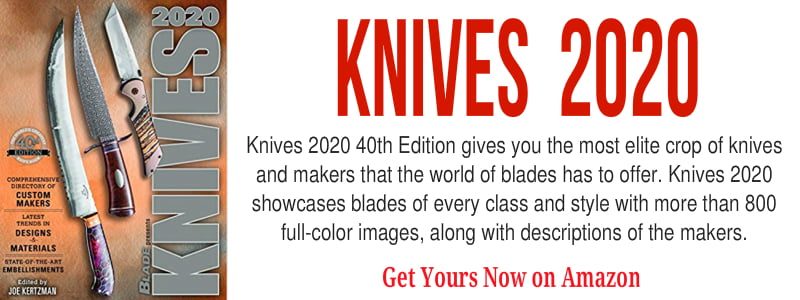
Shopping for a Knife?
Support The Knife Junkie Podcast and YouTube Channel by buying through my affiliate links
Shop on Amazon
Shop on eBay
Shop on Blade HQ
Shop on Field Supply
Shop on Knives Ship Free
Follow The Knife Junkie
Visit The Knife Junkie website
The Knife Junkie Listener Line — 724-466-4467
Email The Knife Junkie
Follow The Knife Junkie on YouTube
Follow The Knife Junkie on Instagram
Follow The Knife Junkie on Twitter
Join The Knife Junkie Facebook Group
Affiliate Disclosure
In the name of full transparency, please be aware that this website contains affiliate links and any purchases made through such links will result in a small commission for me (at no extra cost for you). If you use these links, I might be rewarded credit or a small commission of the sale. If you don’t want to use these links, no problem. But know that I truly do appreciate your support.